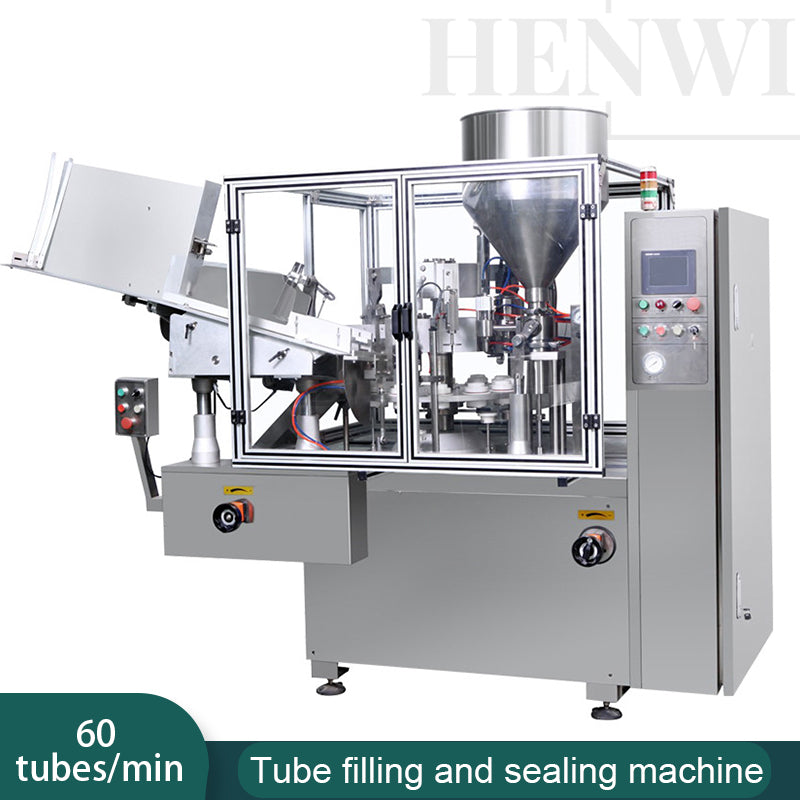
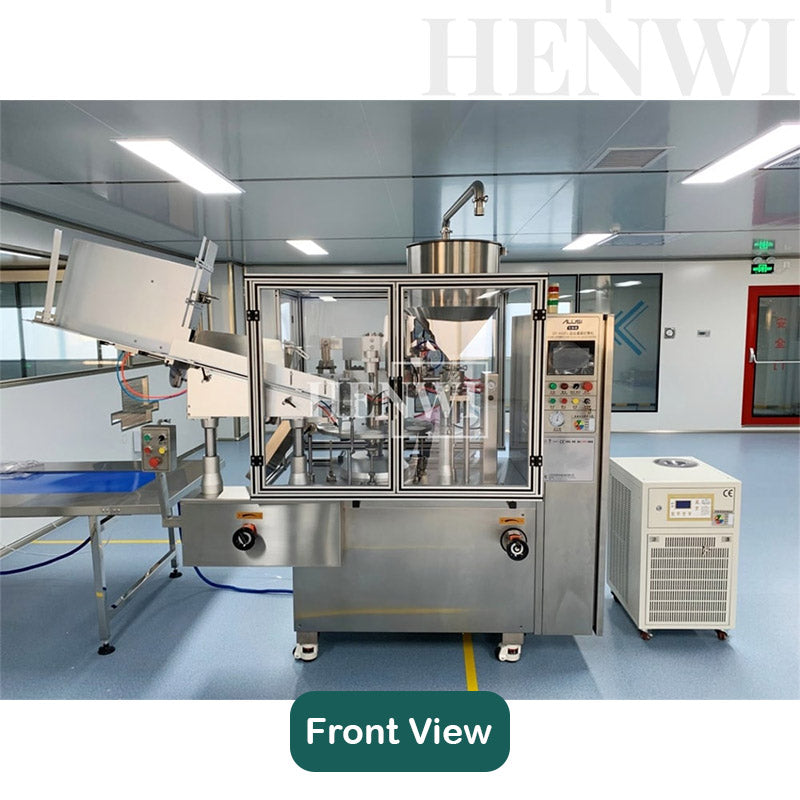
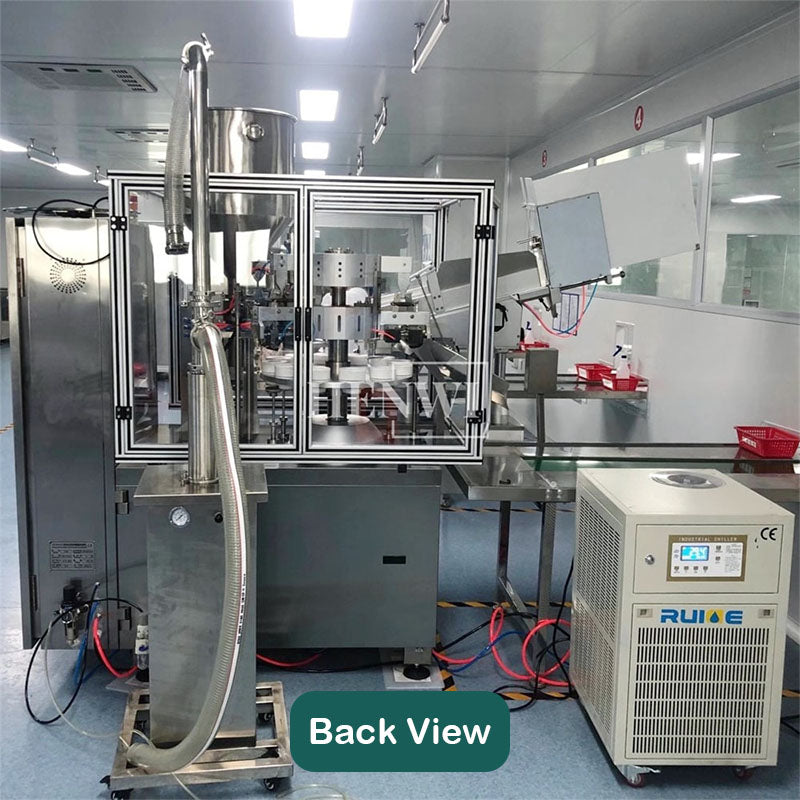
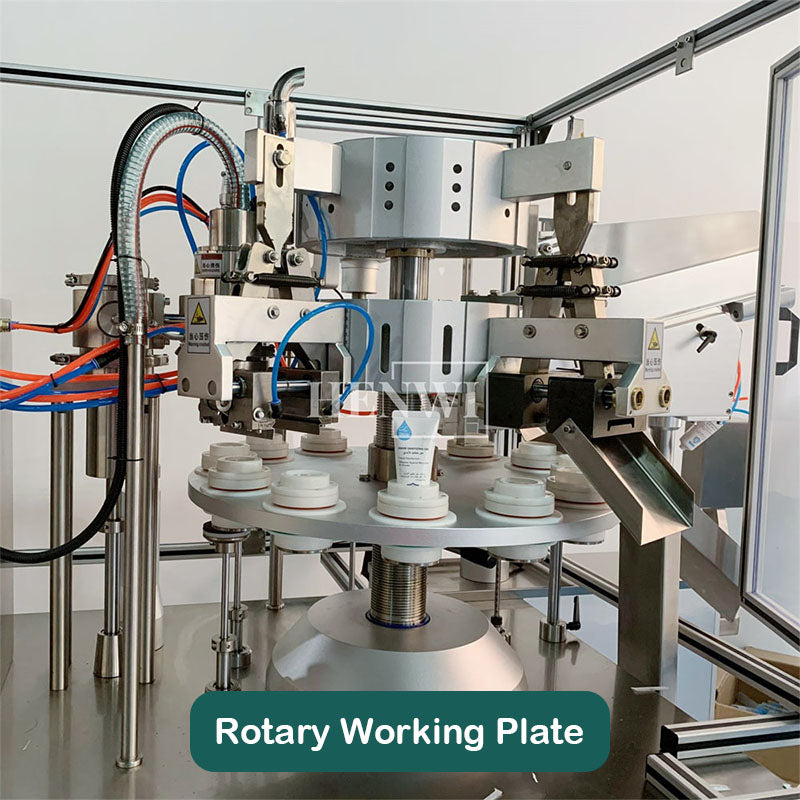
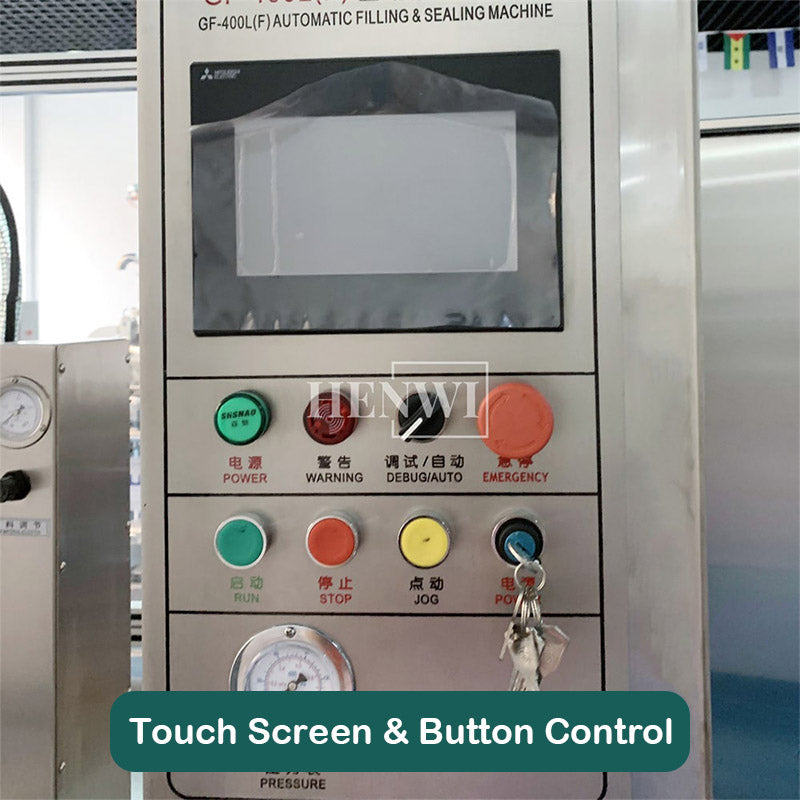
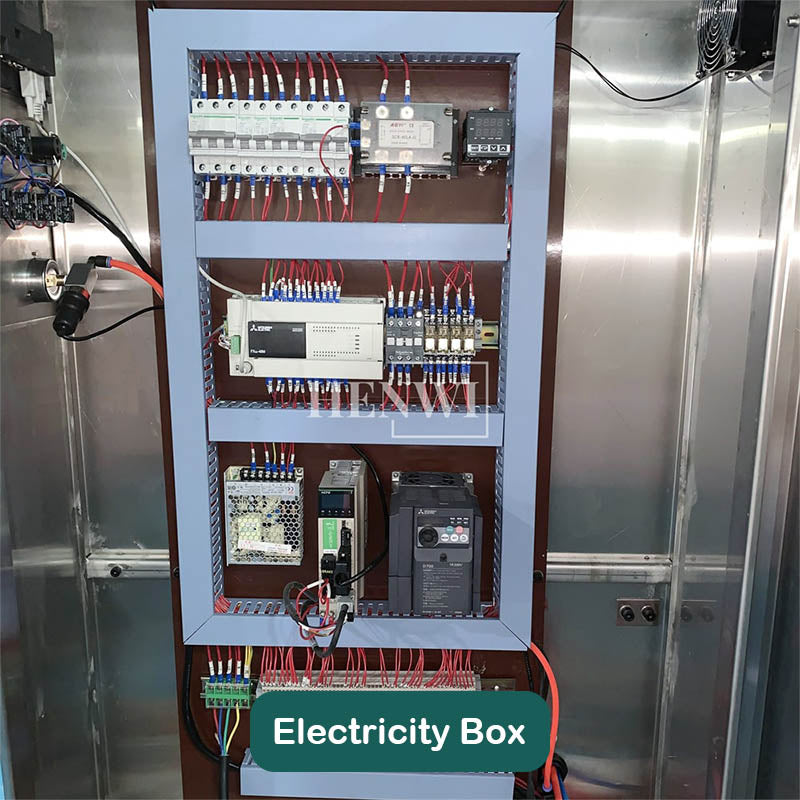
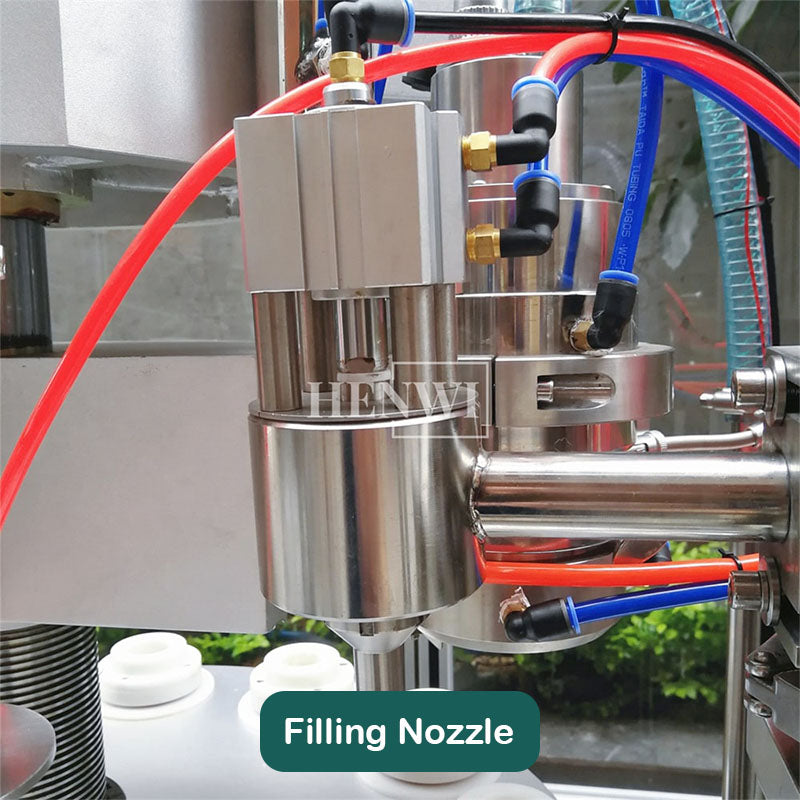
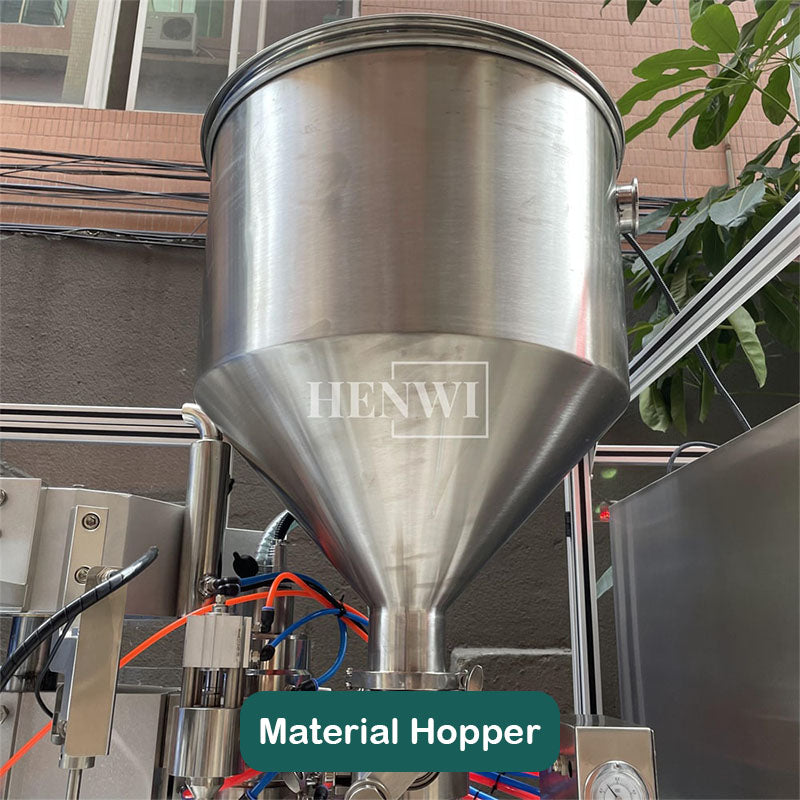
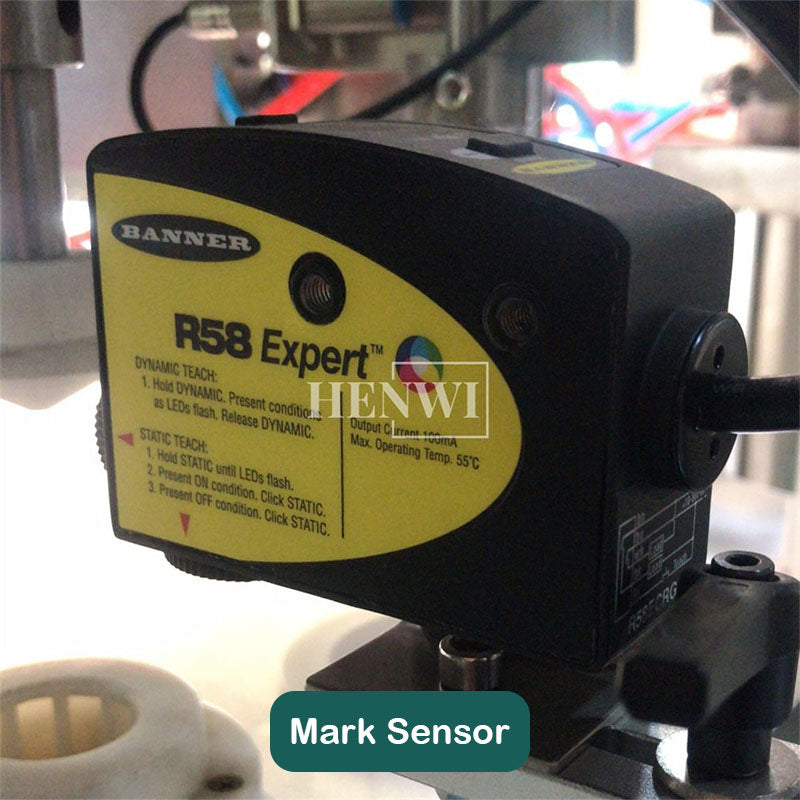
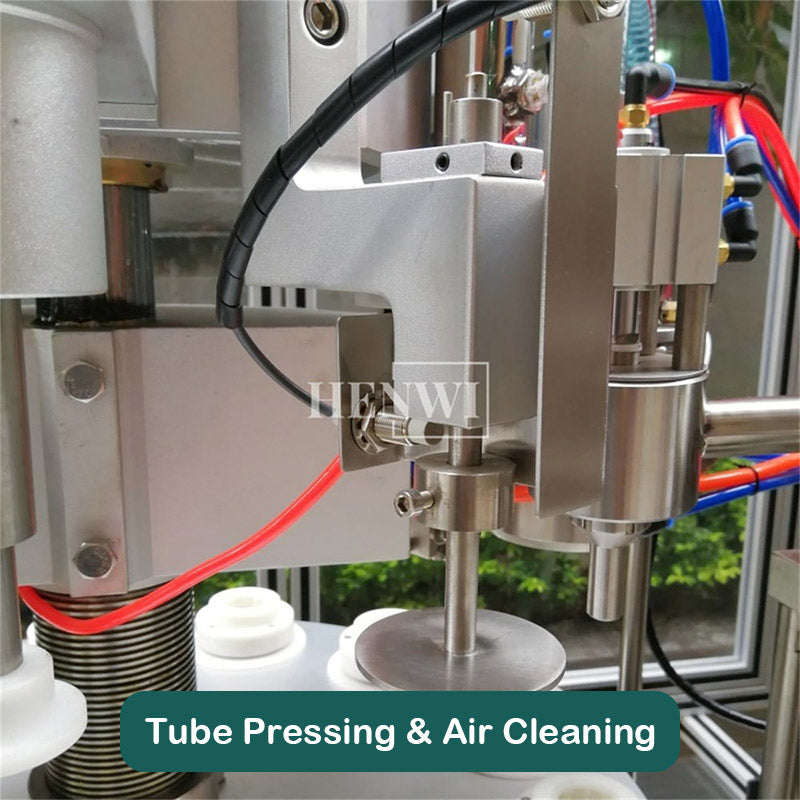
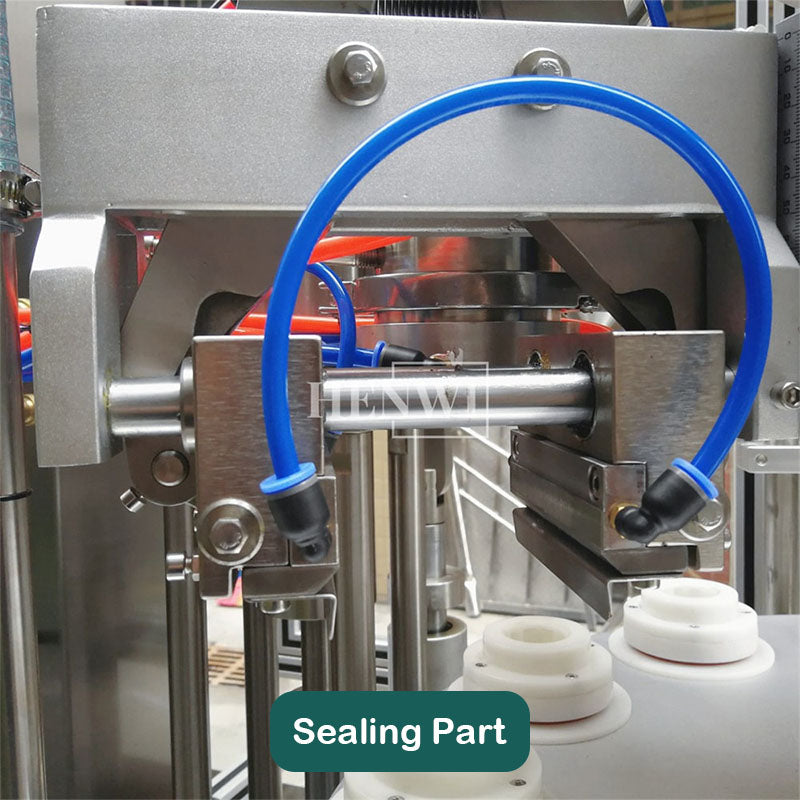
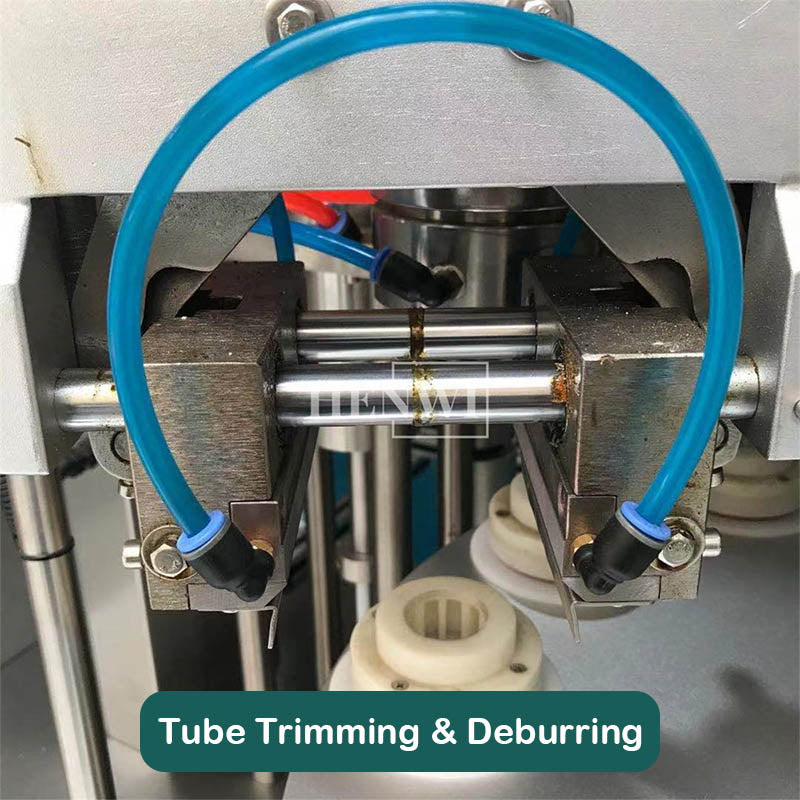
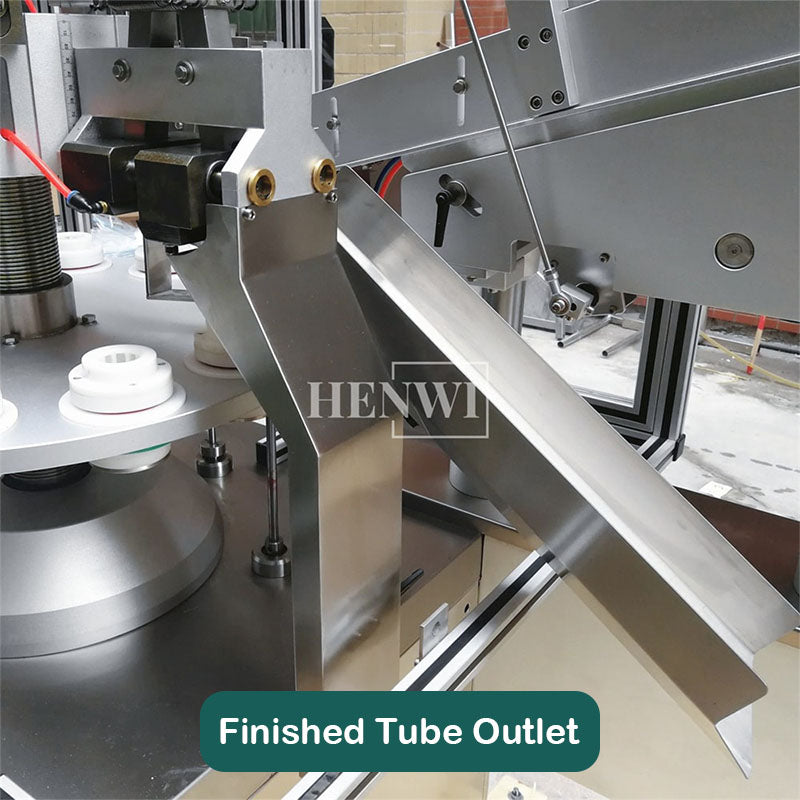
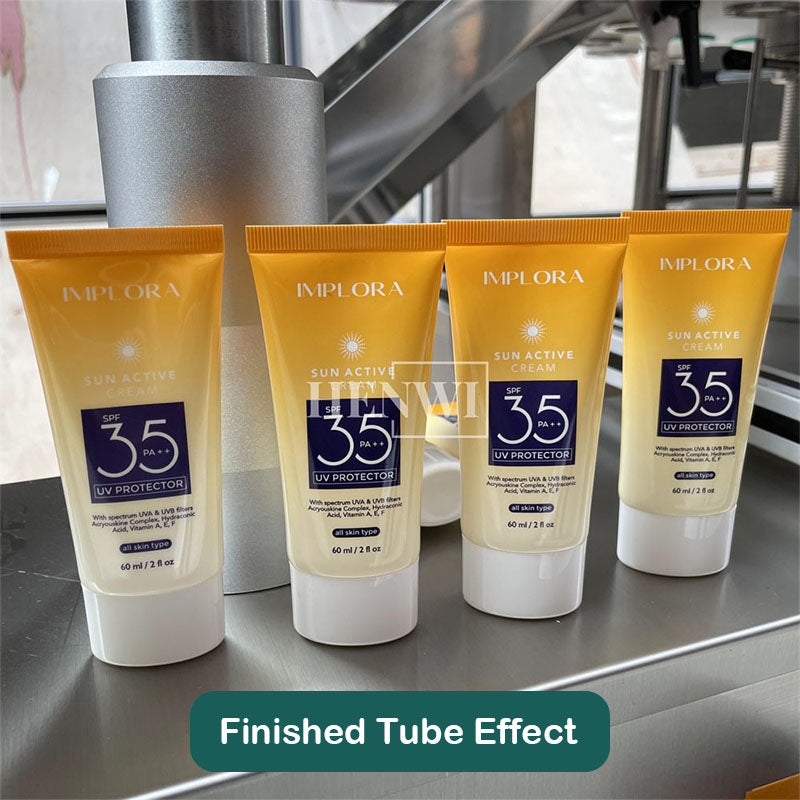
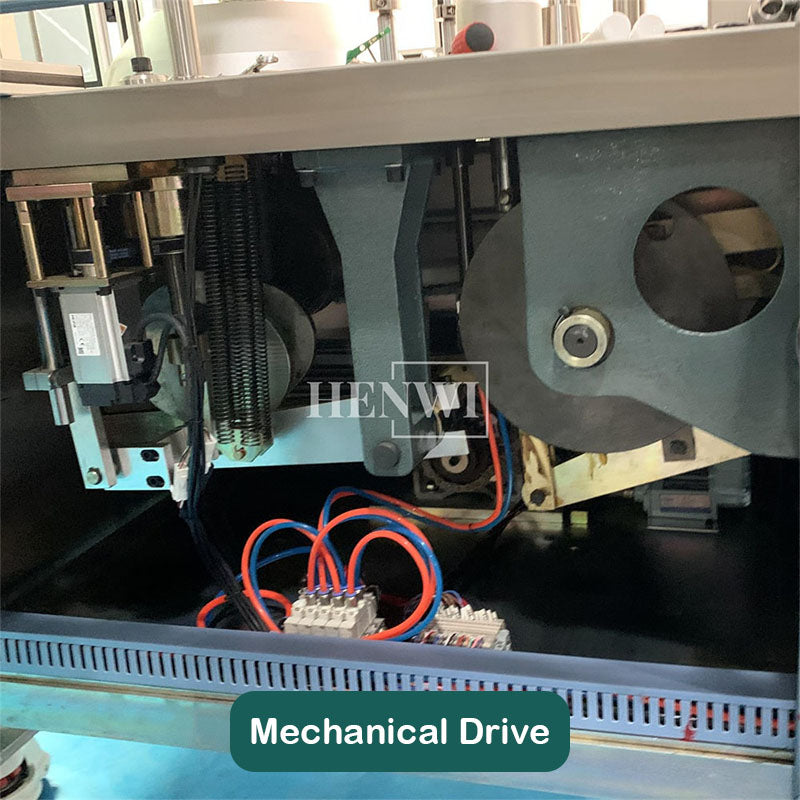
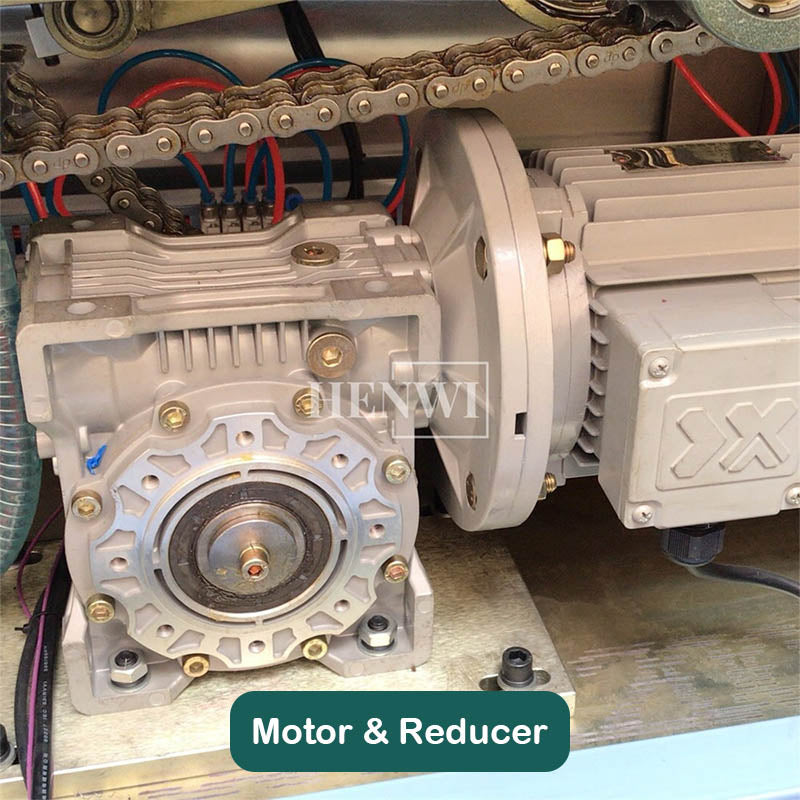
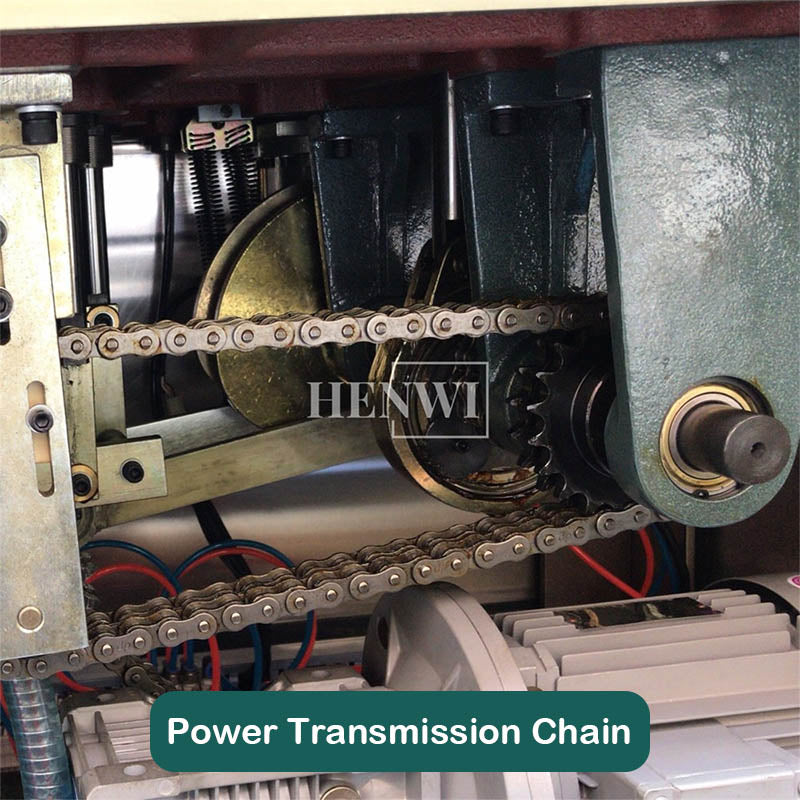
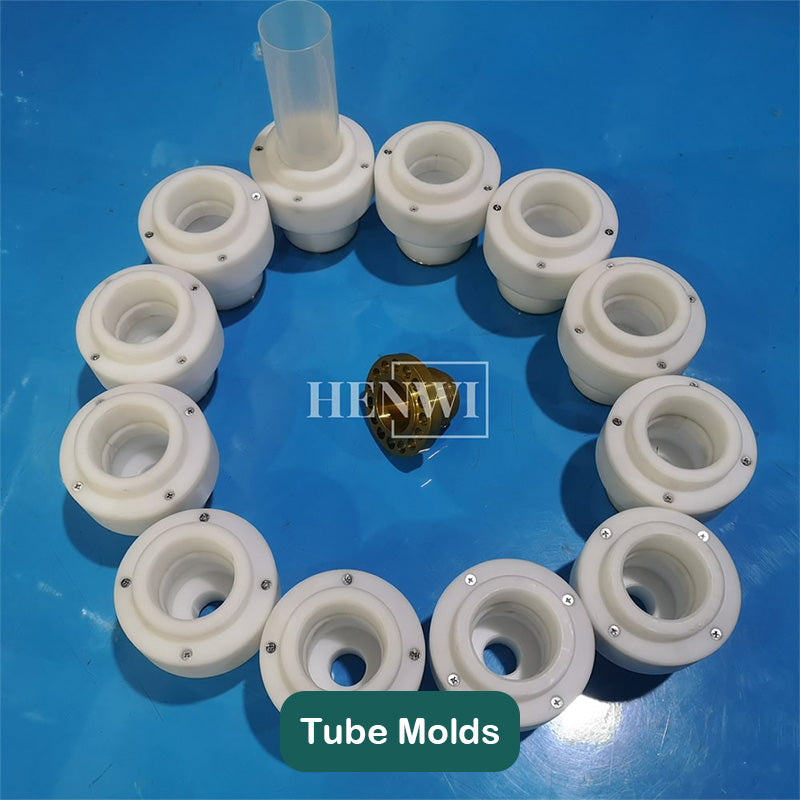
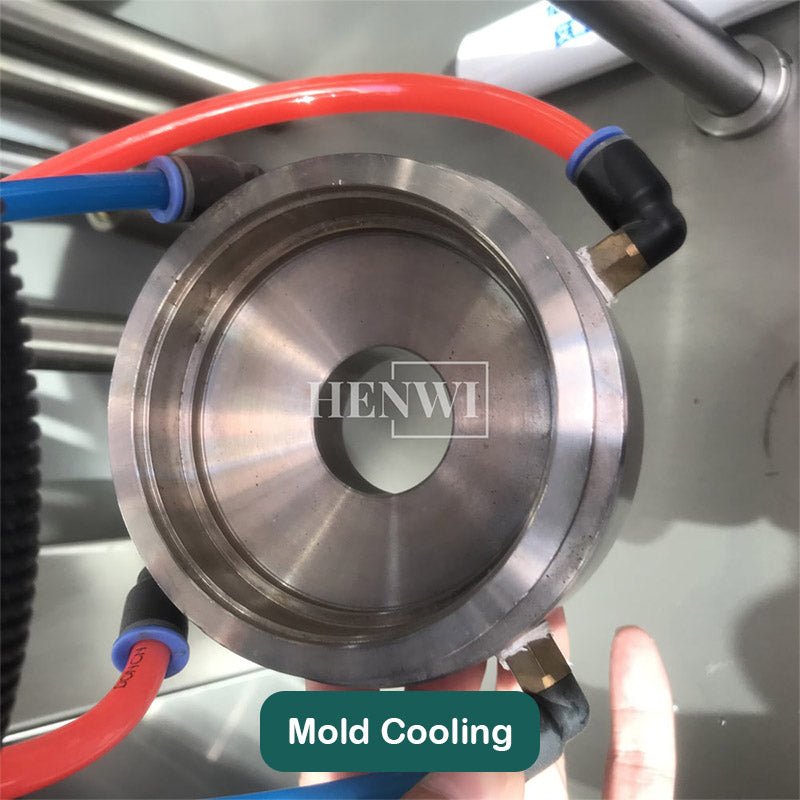
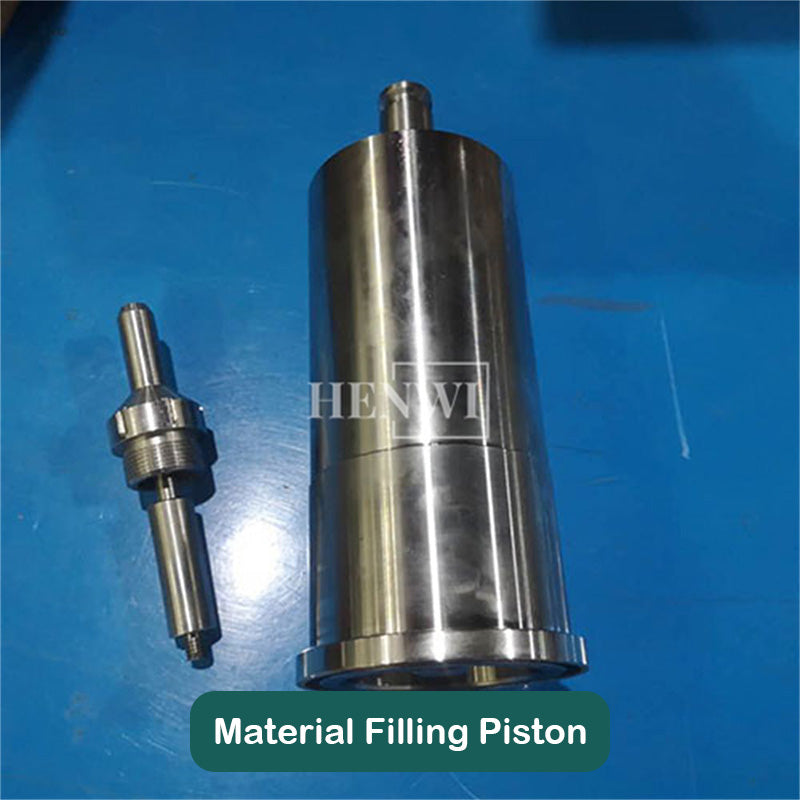
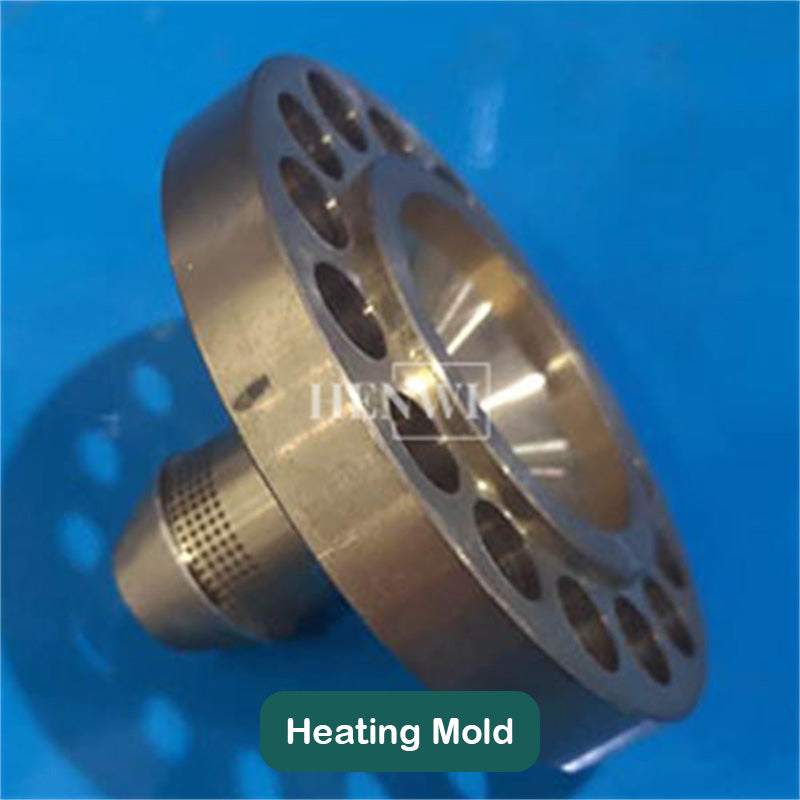
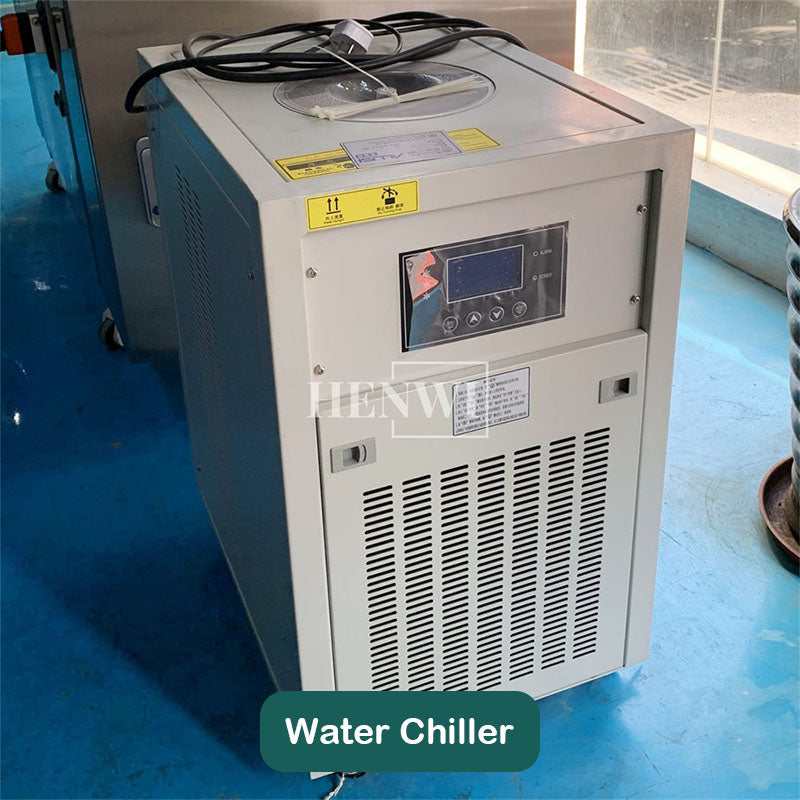
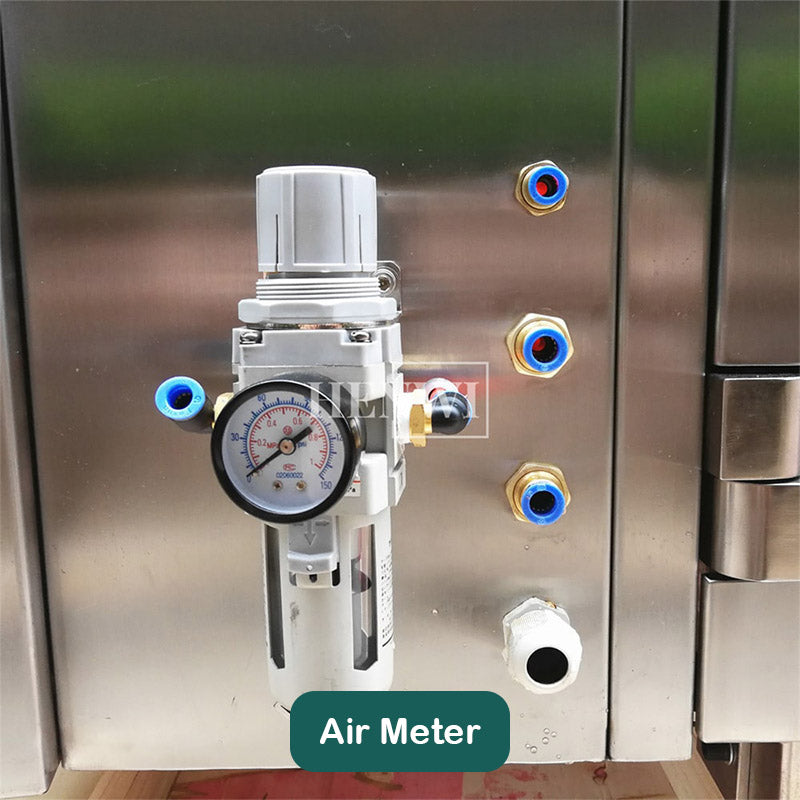
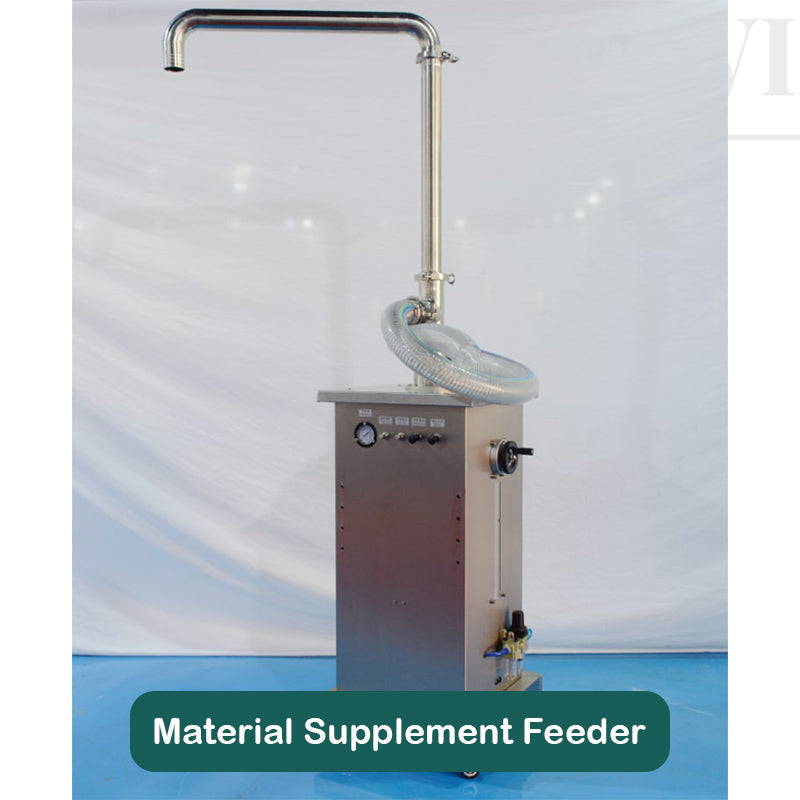
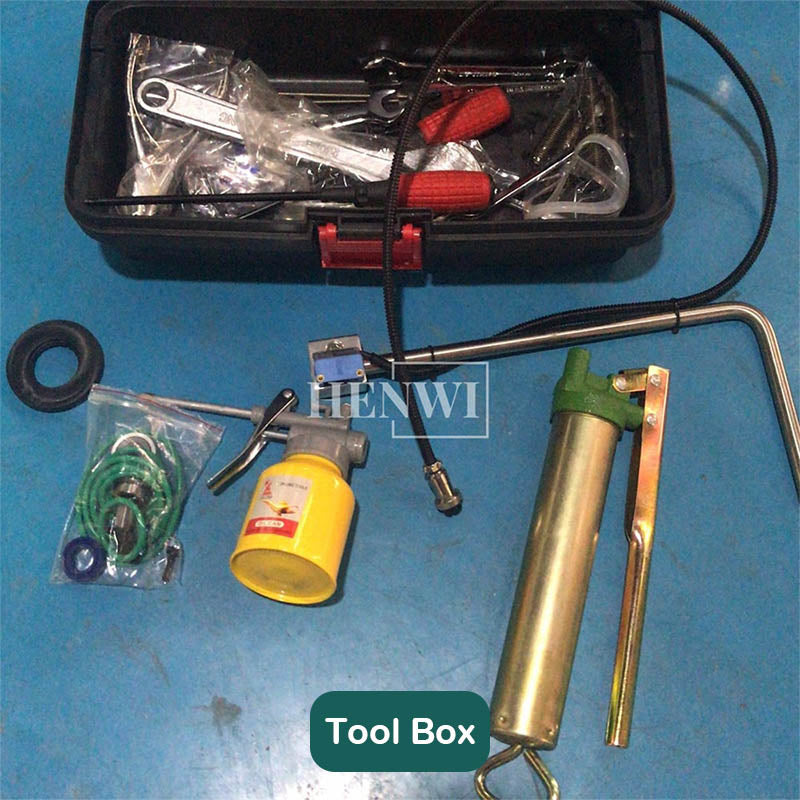
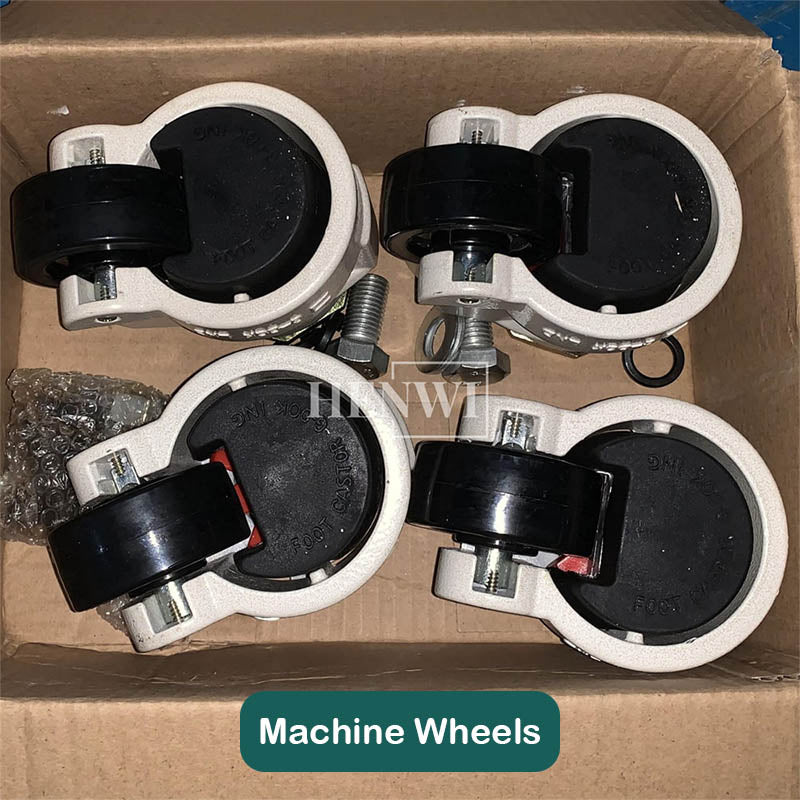
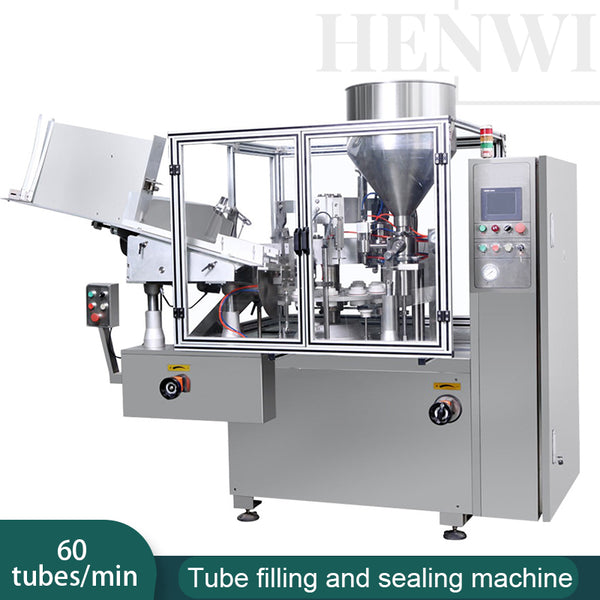
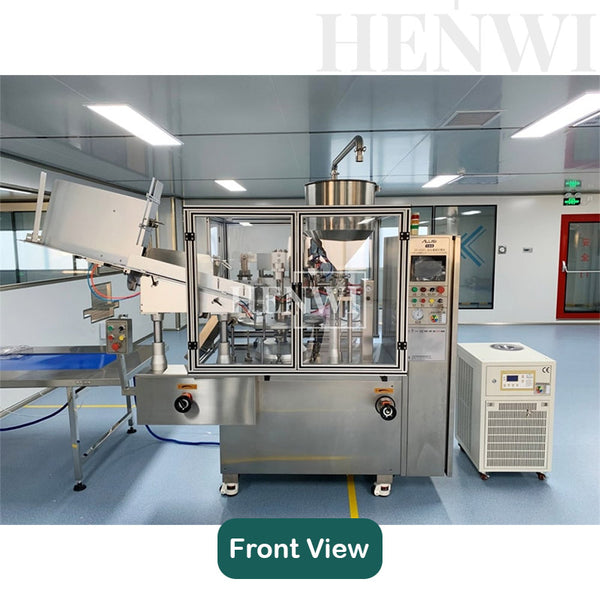
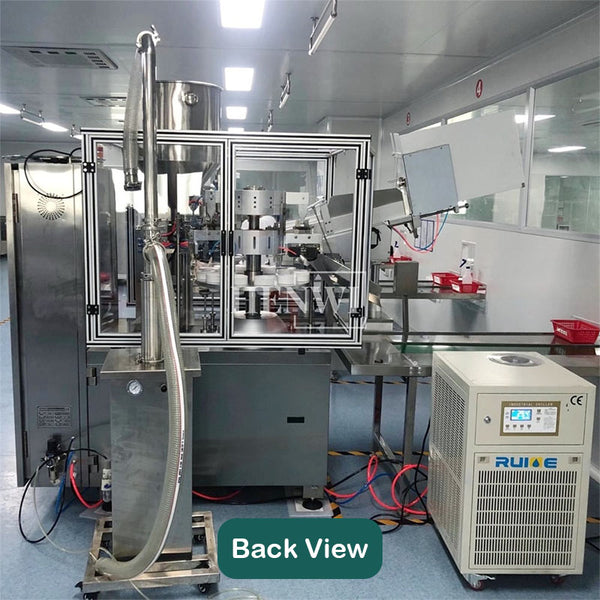
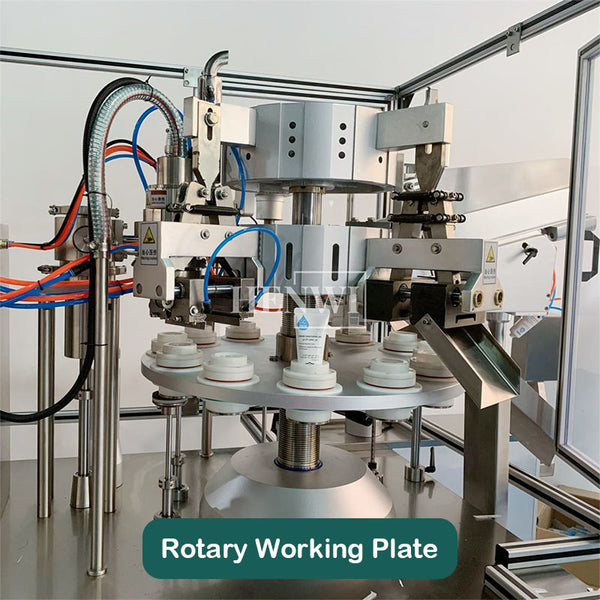
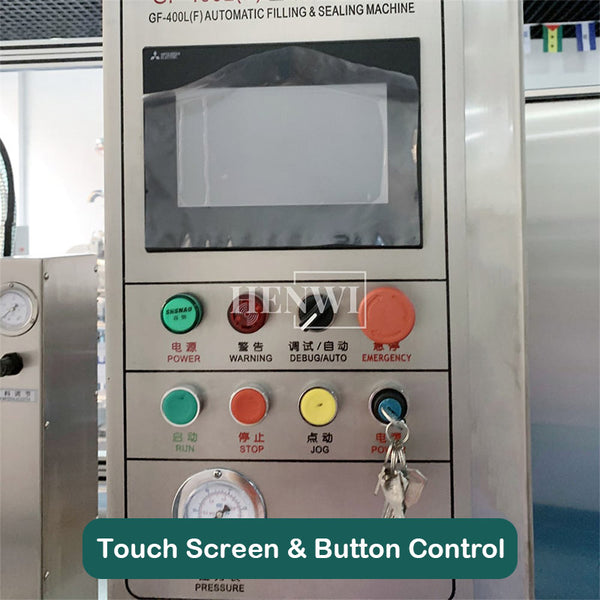
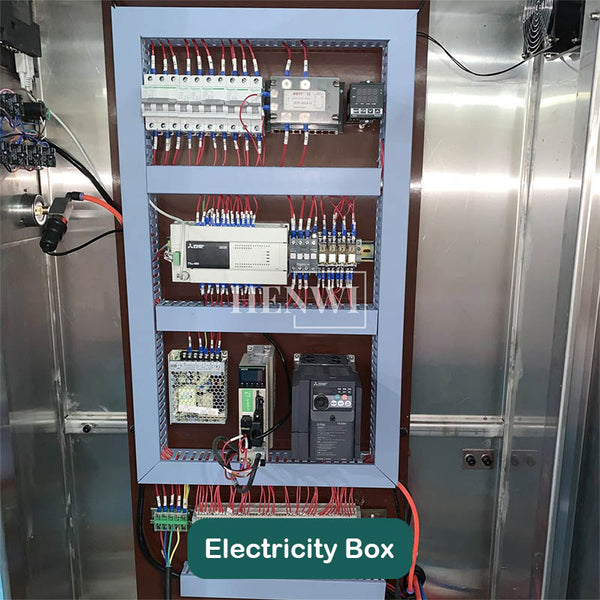
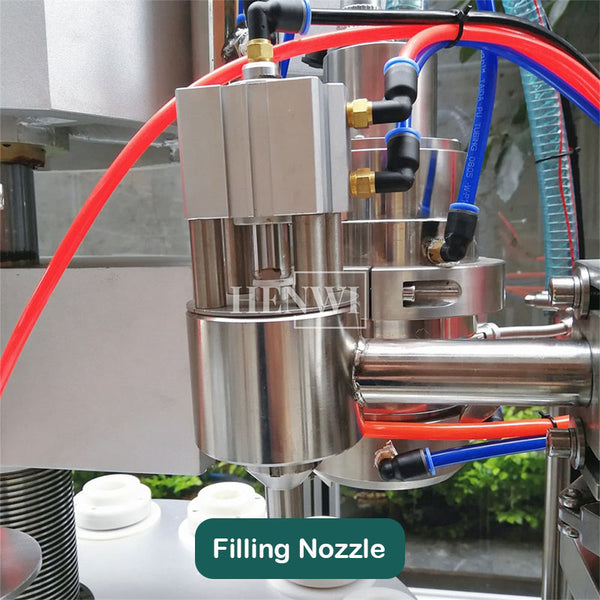
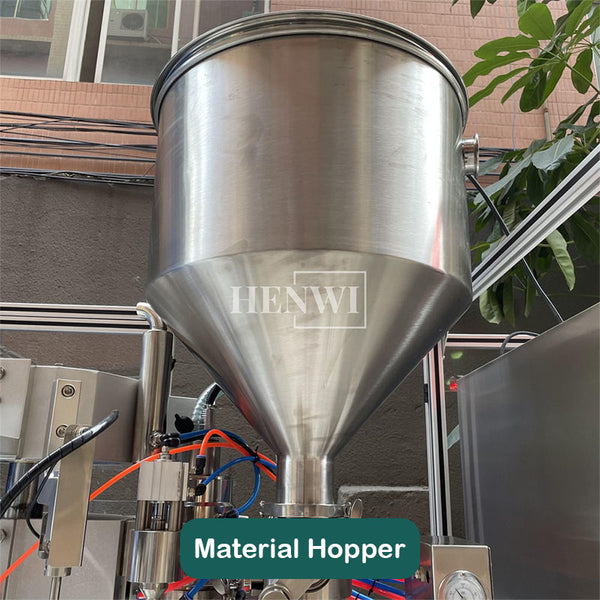
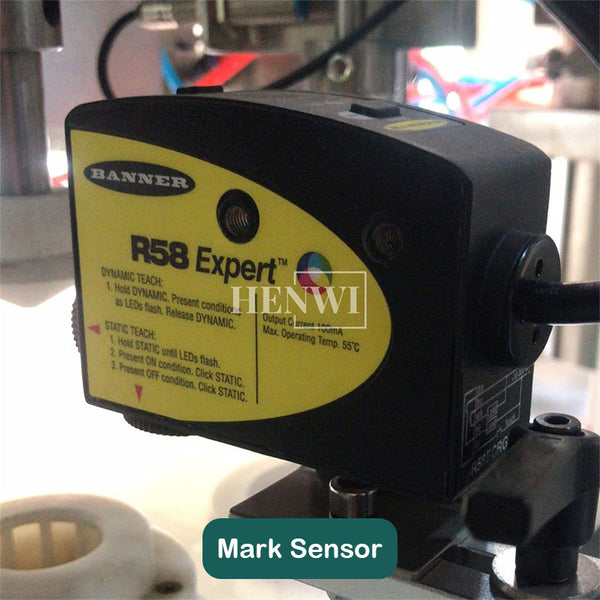
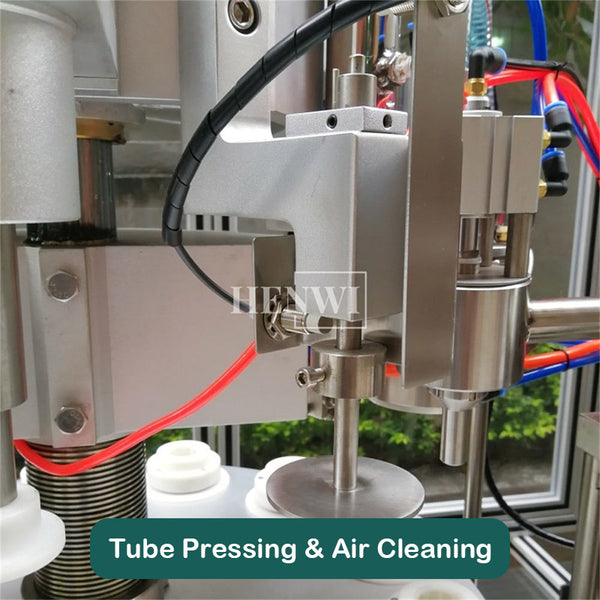
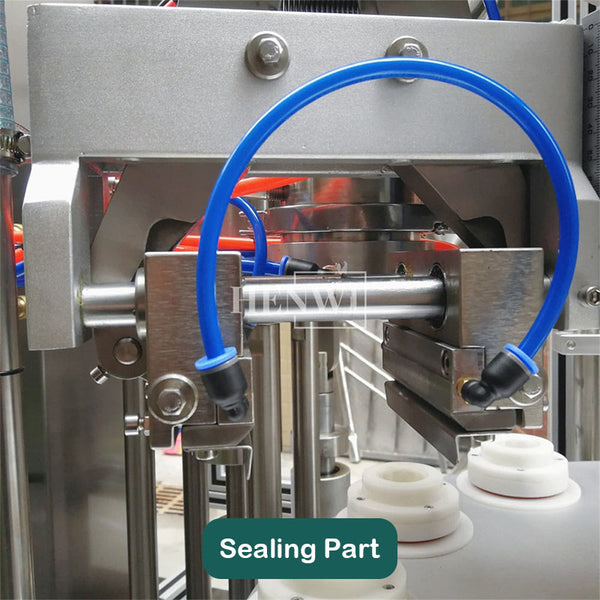
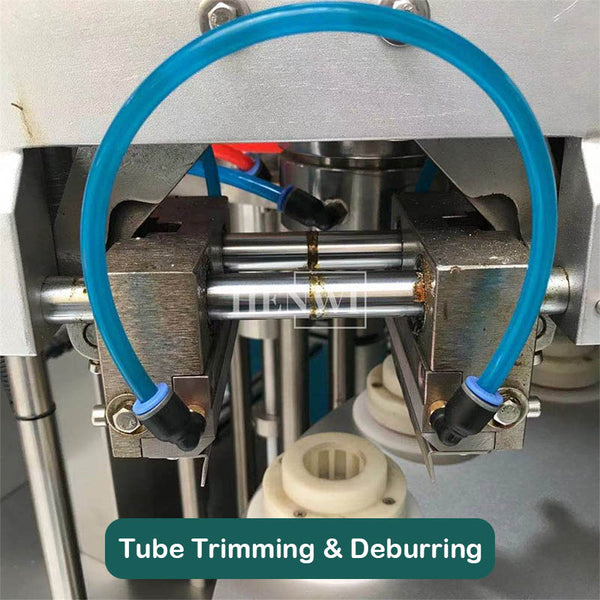
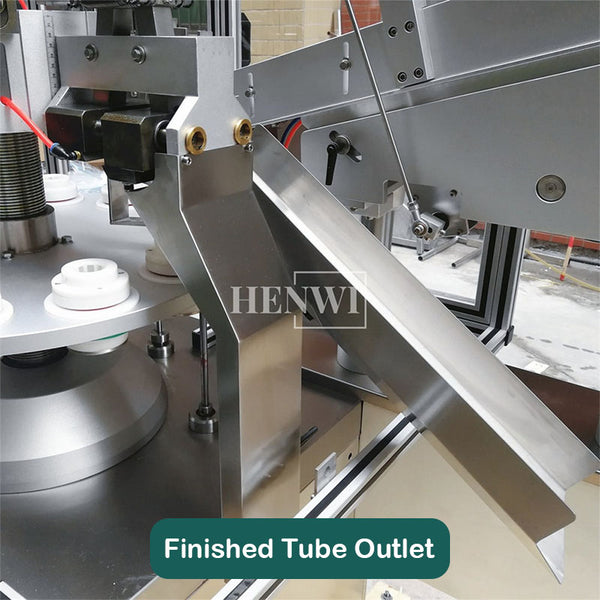
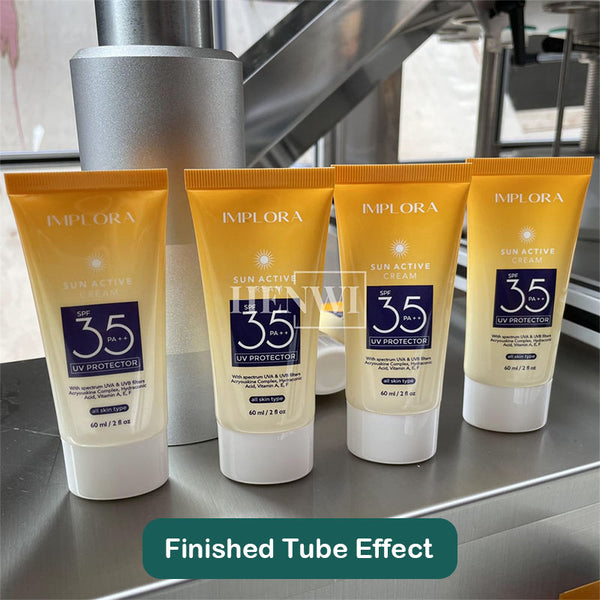
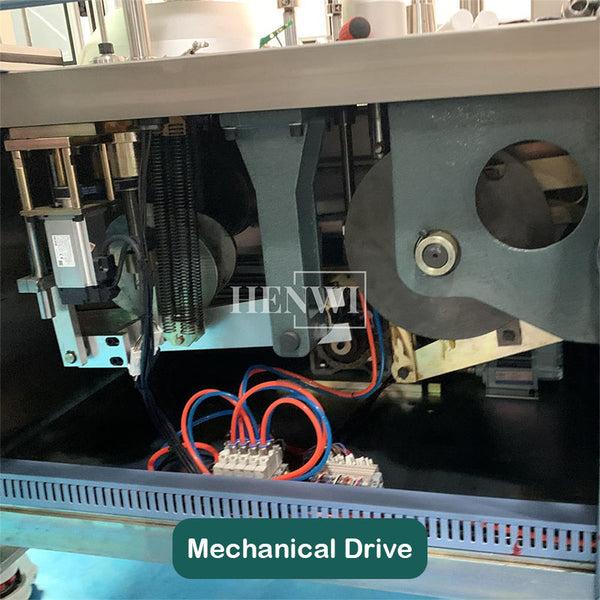
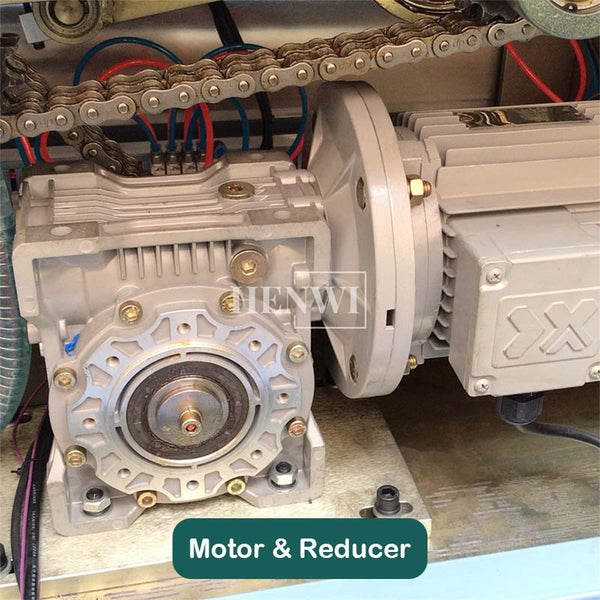
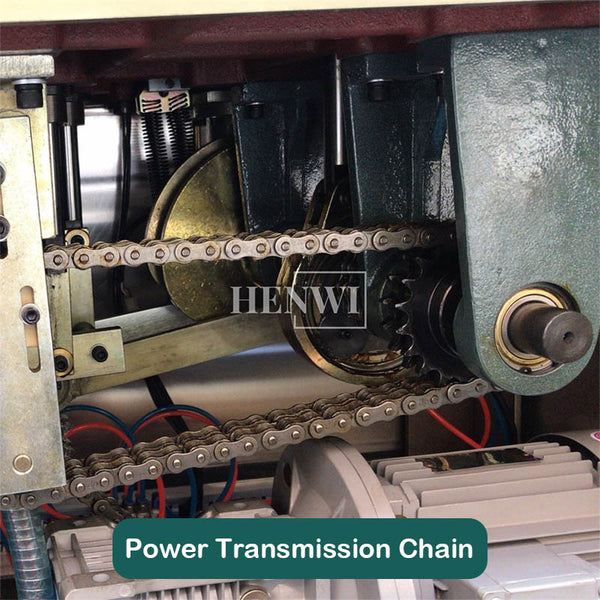
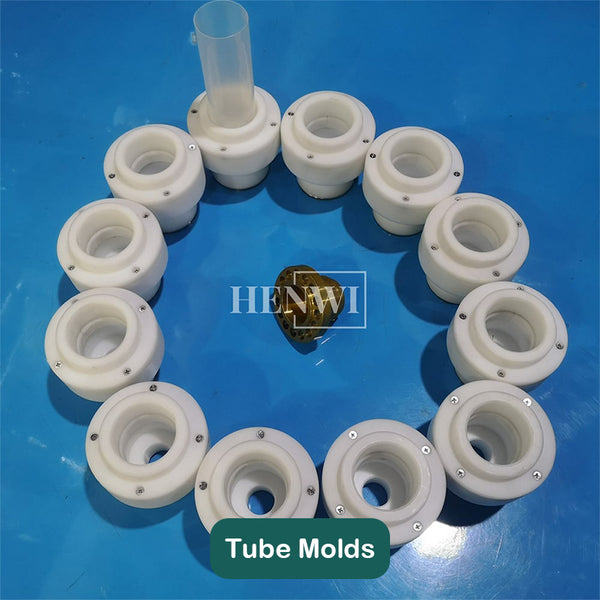
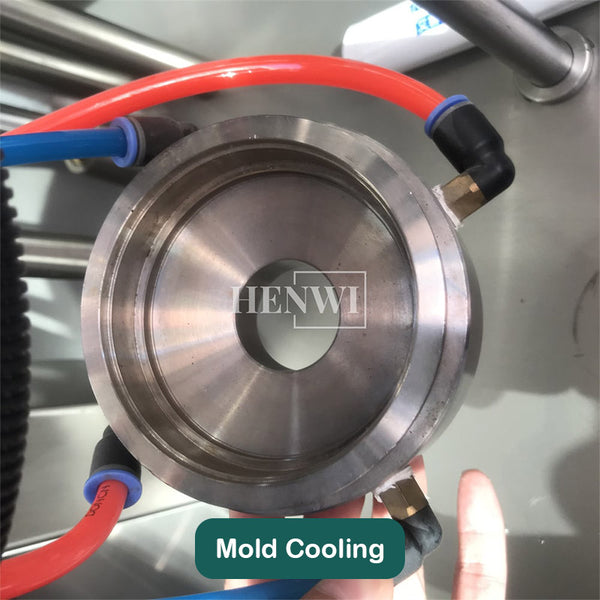
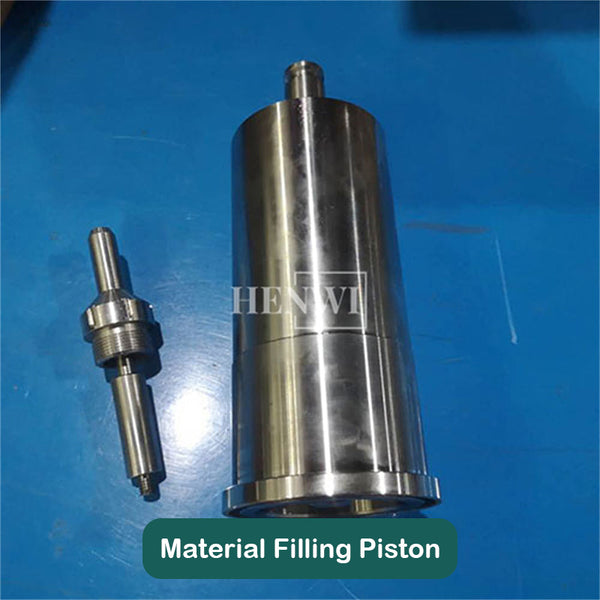
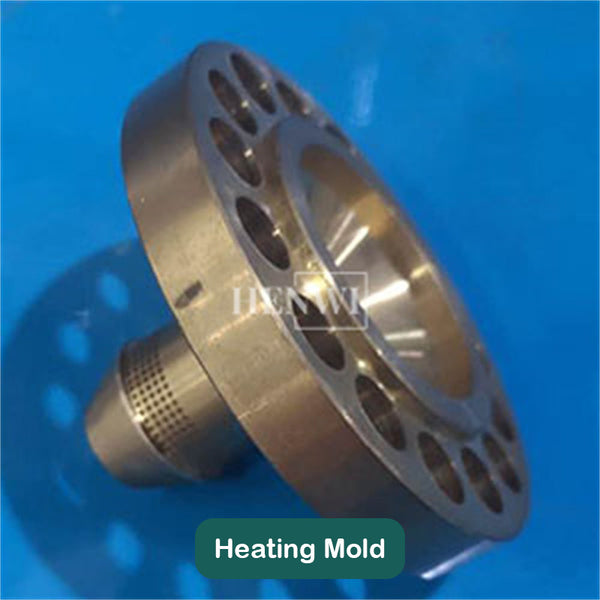
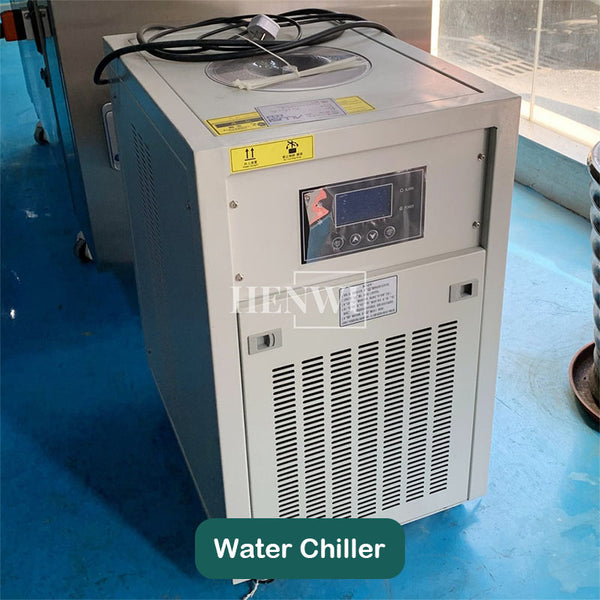
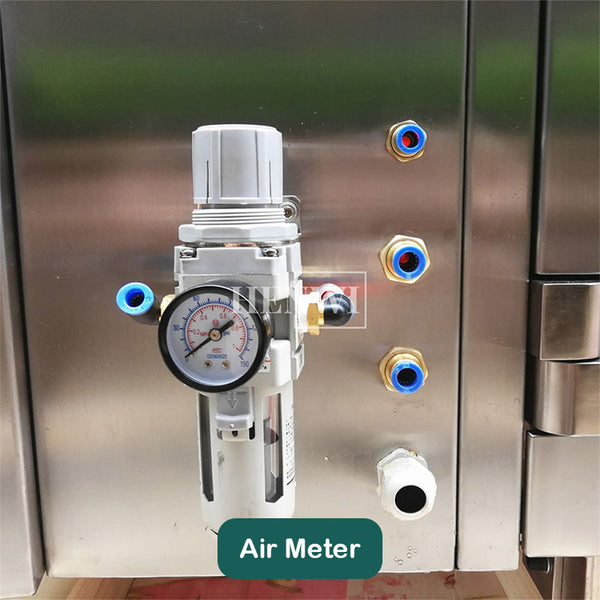
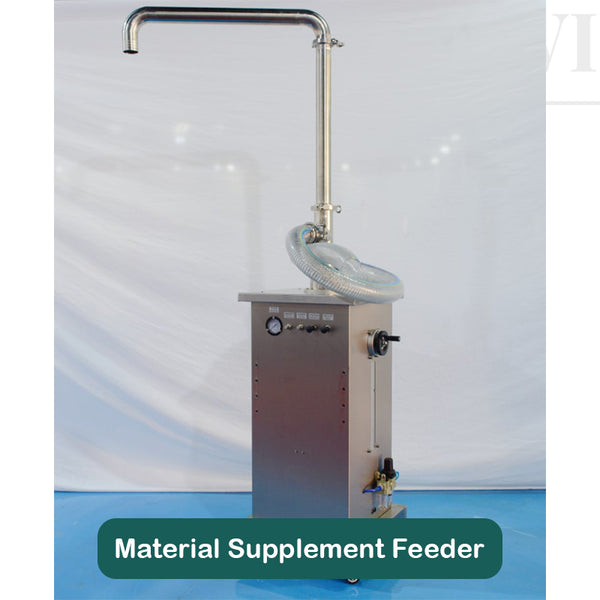
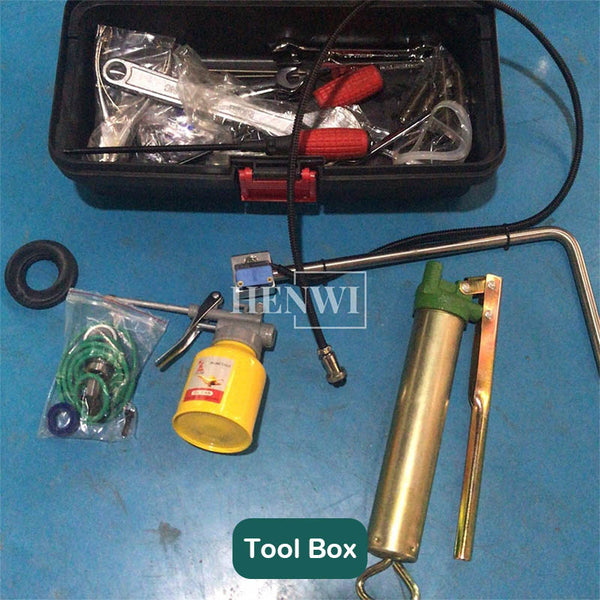
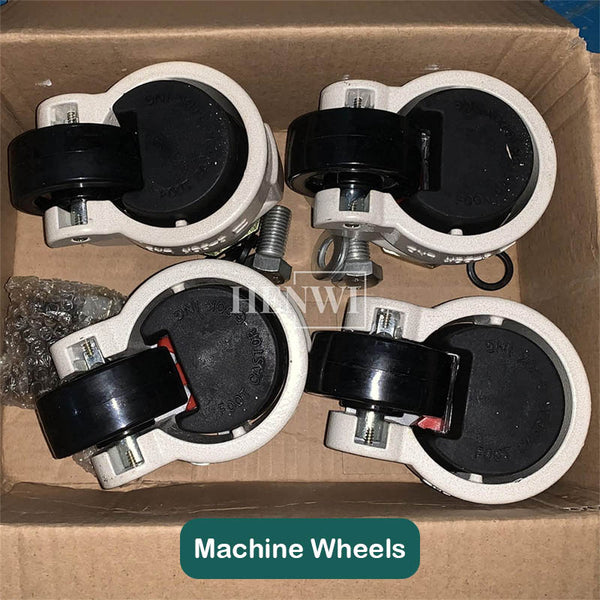
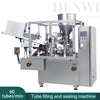
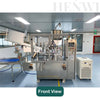
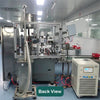
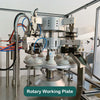
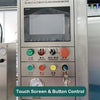
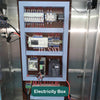
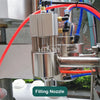
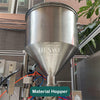
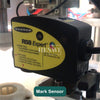
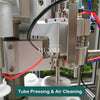
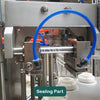
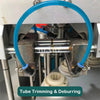
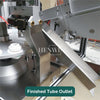
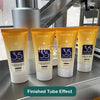
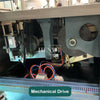
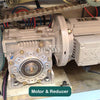
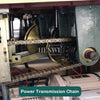
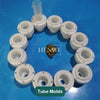
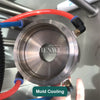
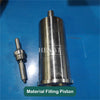
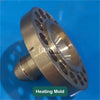
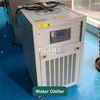
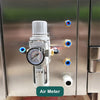
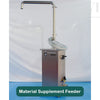
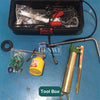
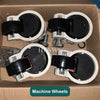
Automatic hot air tube filling and sealing machine
- Цена
- $19,600
The fully automatic tube filling and hot air sealing machine is designed to handle precise filling and sealing operations for soft tubes in industries such as cosmetics, pharmaceuticals, food, and chemicals. This high-performance equipment automates the process from tube feeding, filling, hot air sealing, and trimming, to product ejection, ensuring efficiency and quality in each step.
Key Features and Functionalities:
Automatic Tube Feeding: Equipped with an intelligent tube sorting and feeding system, the machine automatically loads tubes into the designated holders, streamlining the setup process for high-speed production lines. It supports various tube materials, including plastic, laminated, and metal tubes.
Accurate Dosing and Filling System: The filling unit is driven by a precision pneumatic system, offering adjustable dosing volumes with high accuracy (up to ±0.5%). It accommodates a wide range of viscosities, making it suitable for creams, gels, pastes, and other semi-viscous products.
Hot Air Sealing Technology: Utilizing advanced hot air sealing technology, the machine ensures airtight and aesthetically pleasing seals on each tube. The hot air system heats the interior of the tube, melting the plastic and providing a strong, durable seal without compromising the product’s integrity.
Tail Trimming and Coding Options: Post-sealing, the machine automatically trims excess material for a neat, consistent appearance. It also includes options for embossing or inkjet printing codes, dates, or batch numbers on the tube, ensuring traceability and compliance with industry standards.
User-Friendly Control System: The machine is operated via a modern PLC with a touch-screen interface, allowing operators to adjust filling volume, sealing temperature, and production speed easily. The system includes memory functions for different product specifications, allowing quick and efficient changeovers.
Precision Tube Alignment and Positioning: With photoelectric sensors and automated tube orientation, the machine ensures that each tube is correctly positioned before filling and sealing, reducing waste and enhancing output quality.
Hygienic, Durable Construction: Constructed from stainless steel and corrosion-resistant materials, the machine adheres to GMP and FDA standards for hygiene and safety, making it ideal for sensitive products. Its design is easy to clean and maintain, minimizing downtime and maximizing operational efficiency.
Safety and Fault Detection: The machine includes multiple safety features such as overload protection, emergency stop functions, and automatic fault detection systems. In the event of a fault, the machine pauses and displays the issue on the control panel, allowing operators to address it promptly.
Application and Benefits:
This fully automatic tube filling and hot air sealing machine is ideal for large-scale production facilities where efficiency, accuracy, and product integrity are crucial. By automating the entire process, it reduces labor costs, minimizes product waste, and ensures consistent, high-quality output with every cycle. The machine is versatile enough to handle a variety of tube sizes and fill materials, providing exceptional flexibility to meet diverse production needs.
Parameter
Tube type: Plastic tube, Multiple tube |
Filling range: A.6-60ml, B.10-120ml, C.25-250ml, D.50-500ml |
Sealing type: Heating sealing |
Capacity: 1800-4200 tubes/hour |
Number of work positions: 12 |
Safety protection: overload protection |
Filling nozzle: Anti-drop |
Filling accuracy: ±1% |
Sealing shape: Flat tail, curved tail, special-shaped tail |
Applicable tube diameter: 12-50mm |
Applicable tube height: 50-250mm |
Automatic detection function: No work without tube |
Tube loding: Automatic |
Air pressure: 0.6-0.7Mpa |
Air comsumption: 0.3m3/min |
Power: 3KW |
Voltage: 380V/50Hz |
Air consumption: 1-3m³/min |
Machine size: 2600×1250×1980mm |
Machine weight: 1100kgs |
Touch screen: Mitsubishi |
PLC: Mitsubishi |
Sensor: Banner/OMRON/Panasonic |
Inverter: Mitsubishi |
Heater: (400F ) SWITZERLAND |
Temperature controller: (400F ) DELTA |
Pneumatic components: AirTac Taiwan |
Electrical components: Delixi, CHNT, Schneider |
Rotary Worktable
This rotary worktable system integrates multiple processes into a streamlined, automated workflow, including:
Tube Feeding: Automated placement of tubes onto the worktable.
Positioning: Precise alignment of tubes for accurate processing.
Filling: Dispenses product into tubes with precise volume control.
Heating: Utilizes hot air for pre-heating the tube ends for sealing.
Sealing: Ensures secure, airtight sealing of tube ends.
Coding: Applies batch codes or production information onto the tube.
Cutting: Trims excess material from the tube end post-sealing.
Ejection: Releases finished tubes from the worktable for collection.
1. Tube Feeding
The Tube Feeding system automates the process of placing empty tubes onto the worktable. Equipped with a tube sorting mechanism, this system ensures each tube is positioned upright and in the correct alignment for subsequent processing. It increases production efficiency by reducing manual handling, providing a smooth workflow for high-speed operations.
2. Positioning
The Positioning mechanism utilizes sensors to accurately align each tube before filling. This guarantees precise label or seam alignment, ensuring that each tube is correctly positioned for the filling, sealing, and coding stages. This process minimizes errors, reduces material waste, and ensures uniform output quality.
3. Filling
The Filling system is designed to handle a variety of product consistencies, from liquids to thick creams. With precise volumetric controls, the filling nozzle dispenses the exact amount of product required, reducing overfill or underfill. It supports a range of filling volumes to meet various production needs and ensure consistent, accurate filling every time.
4. Heating
The Heating unit uses hot air technology to pre-heat the open end of each tube before sealing. This step is critical for melting and softening the tube’s plastic, preparing it for a strong, airtight seal. This system maintains a consistent temperature to ensure optimal bonding without damaging the tube material.
5. Sealing & Coding
The Sealing mechanism compresses the heated tube ends, creating a tight and durable seal. This ensures that the product is securely contained within the tube, preventing leaks and preserving product integrity. The sealed edges are smooth and professional, meeting quality standards across industries.
The Coding unit applies batch numbers, expiration dates, or other important information directly onto each tube. This can be done via embossing. Coding ensures product traceability and regulatory compliance, providing essential information for quality control.
6. Cutting
The Cutting system trims excess material from the sealed end of each tube, providing a neat, uniform appearance. This process enhances the final presentation of the product while ensuring that all tubes have a consistent, professional finish, ready for retail packaging.
7. Ejection
The Ejection mechanism safely releases the processed tube from the worktable into a collection bin. This automated ejection ensures that each tube is promptly removed after processing, allowing for uninterrupted operation and reducing manual handling. It maximizes output and maintains a smooth production line.
Touch Screen
The Touch Screen interface offers a user-friendly control panel where operators can monitor and adjust machine settings, including speed, volume, temperature, and coding parameters. It also features error detection and diagnostic functions, allowing operators to quickly troubleshoot and maintain optimal machine performance.
Electric Box
The Electric Box houses all of the machine’s electrical components, including circuitry and safety switches. Designed for easy access and maintenance, this box ensures stable power supply and controls the machine’s automation functions. It is equipped with protective features to prevent overload and ensure operator safety.
Material Feeder & Chiller
The Material Feeder provides a steady supply of product material directly to the filling system, ensuring continuous operation and reducing manual refilling needs. With adjustable flow control and a high-capacity hopper, the feeder maintains a consistent supply regardless of material viscosity, from thin liquids to thick pastes. The hopper is designed to minimize material wastage and includes anti-clogging features, guaranteeing smooth, uninterrupted operation during long production runs. The material feeder is also easy to clean, supporting fast changeovers between different products.
The Chiller, or cold water machine, is specifically designed to protect soft tubes from overheating during high-temperature sealing and filling processes. By circulating chilled water around the tubes, the chiller maintains a consistent, low temperature on the exterior surfaces, effectively preventing the soft material from deforming or melting. This precise cooling system is essential for preserving tube integrity and ensuring that the sealing process produces clean, undamaged finishes.
Transmission System
The Transmission System is a crucial component that powers the coordinated movement of the machine’s various stages, including tube feeding, positioning, filling, sealing, and ejection. It operates using precision-engineered gears, belts, and motors to ensure smooth, synchronized motion across all sections of the production line. This system enables accurate timing and alignment of each stage, allowing the machine to operate at high speeds without sacrificing precision.
Built for durability and stability, the transmission system uses high-quality materials and a robust design to withstand long production cycles and heavy-duty operation. With minimal vibration and noise, it ensures steady performance and reduces wear on other machine parts, extending the overall lifespan of the equipment. Additionally, the transmission system includes adjustable speed controls, enabling operators to customize operational speed based on production requirements, enhancing flexibility and efficiency across different product runs.
Mold
Shipping Information
Shipping
In order to offering better service,we have operated with multiple shipping companies like Fedex,DHL,DUP,UPS,EMS etc.We sure that you can choose the most suitable one.For our online products.
1.Most of them will be shipped by express shipping like Fedex or DHL,delivery time is 6-8 business days.
2.Some small products will be sent by regular shipping,delivery time is 15-45 business days.(There is an instruction saying this product will be sent by regular shipping.)But if you need faster shipping,please contact us to upgrade shipping method.We are glad to help you.
3.Some customers can not place their order since there is an error saying that we can not delivery the product to their countries.If you are in this situation,please contact us to confirm the price and shipping,we will help you place the order successfully .The shipping fee is hard to set up online,and in this situation,it is possible to spend less money to get this product,so it will be better if you can contact us.
4.If you find the shipping fee is too expensive for you,please contact us,we are glad to help you find the best shipping method.For large machine,it will be better for you to contact us before placing the order,in this way we can confirm the price,delivery time and check if the machine is really suitable for your products.
Payment
You may find that we only support paypal now,but we can offer other payment method like west union,TT,credit card,wechat pay,Alipay.You will find the best one as your need.If you have any problems about payment,please send us message.Although Some of them are not supported on online service now, we are trying our best to upgrade these.
Product Service
We want you to be happy with your purchase and trying our best to offer the better service to our customers,so we offer some solution if you have below problems or meet below situation: 1. If you received a machine and found the machine was broken :
First,we should note that we will not send any used machine or broken machine to our customers.As we all know,everything will happen during shipping,if your machine is broken,please contact us and help us to complaint this to shipping company.We are here to help you.
2. If you don’t know how to assemble machine or use the machine :
Some of our machine may need you assemble them,or you don’t know how to use the machine,just send us e-mail or message,we will send you video and manual to help you know more about it.
Accuracy, completeness and timeliness of information
We are not responsible for any inaccurate, incomplete or timely information provided on this website. The materials on this website are for general information only and should not be relied upon or used as the sole basis for making decisions without consulting primary, more accurate, complete or timely sources of information. Any reliance on the materials on this website is at your own risk. This website may contain certain historical information. The historical information is not necessarily up to date and is for your reference only. We reserve the right to modify the content of this website at any time, but we are under no obligation to update any information on our website. You agree that it is your responsibility to monitor changes to our website.
Service and price modification
The prices of our products are subject to change without prior notice. We reserve the right to modify or terminate the Services (or any part or content thereof) at any time without notice. We shall not be liable to you or any third party for any modification, price change, suspension or discontinuation of the Services.
Products or Services
Some products or services may be available online only through the website. These products or services may be available in limited quantities and can only be returned or exchanged in accordance with our return policy. We have made every effort to display the colors and images of our products that appear in stores as accurately as possible. We cannot guarantee that any color displayed on your computer monitor is accurate.
HENWI TECHNOLOGY LIMITED
[Re: Privacy Compliance Officer]
Bldg 3, Gaoyi Industrial Park, No.5 Shangbai Rd., 528226 Shishan town, Nanhai Dist, Foshan City, P.R., China
About Us
We are a professional cosmetic, pharm and food machinery production, sales and related technical services of modern high-tech enterprises.