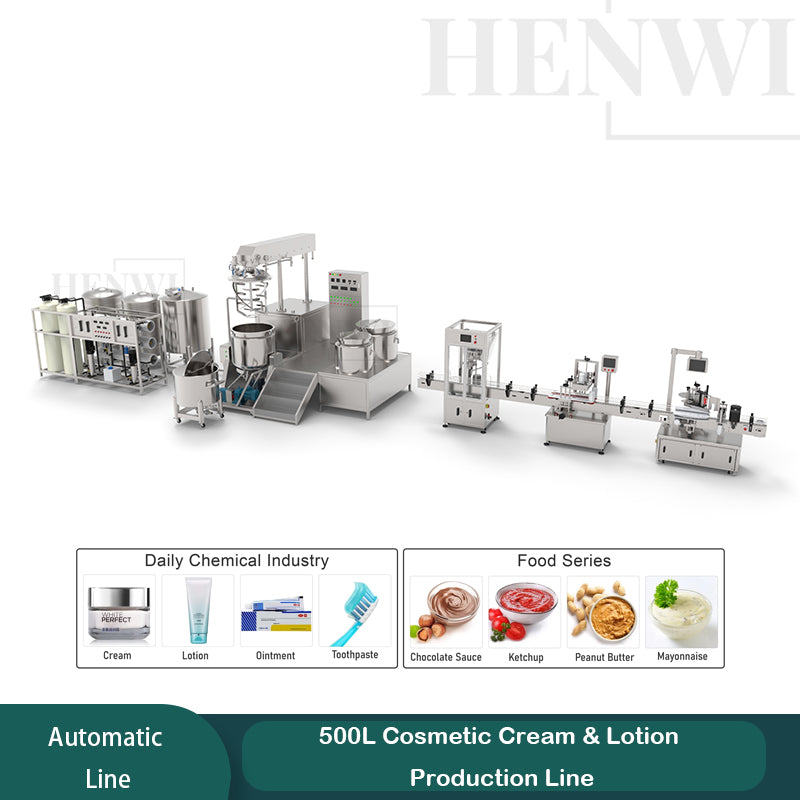
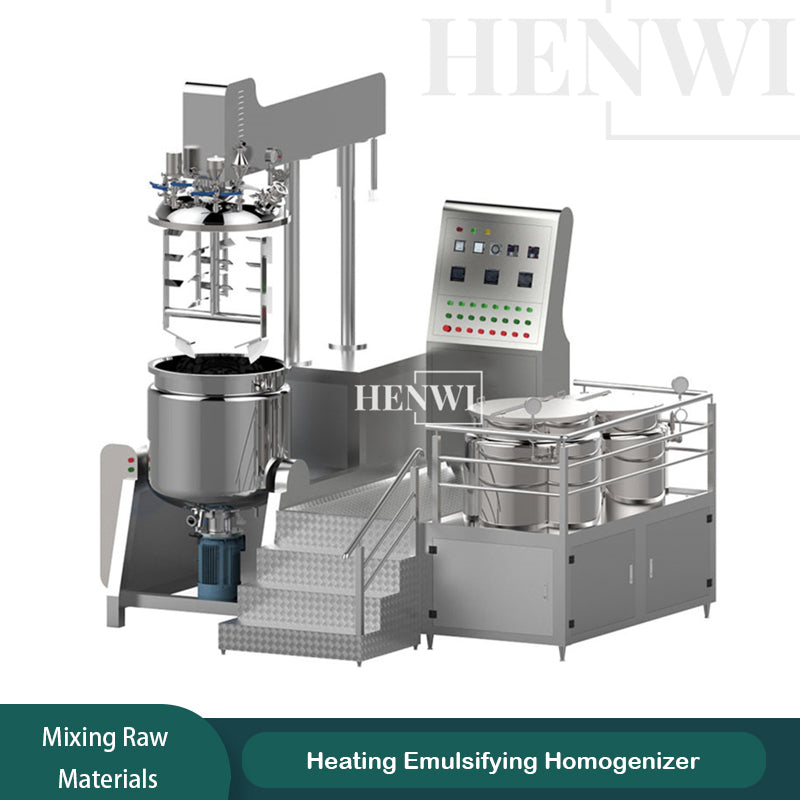
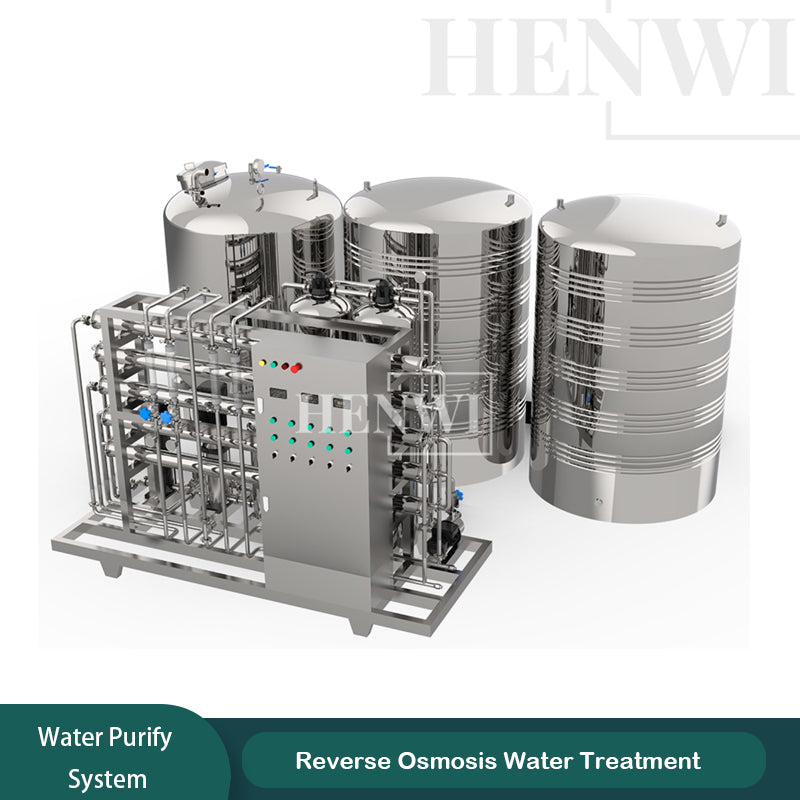
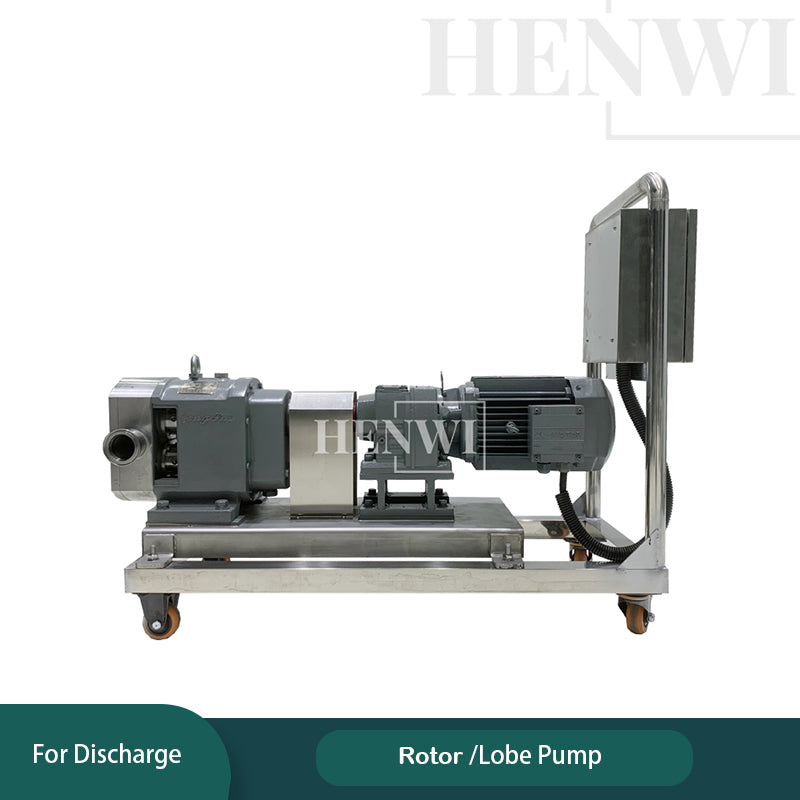
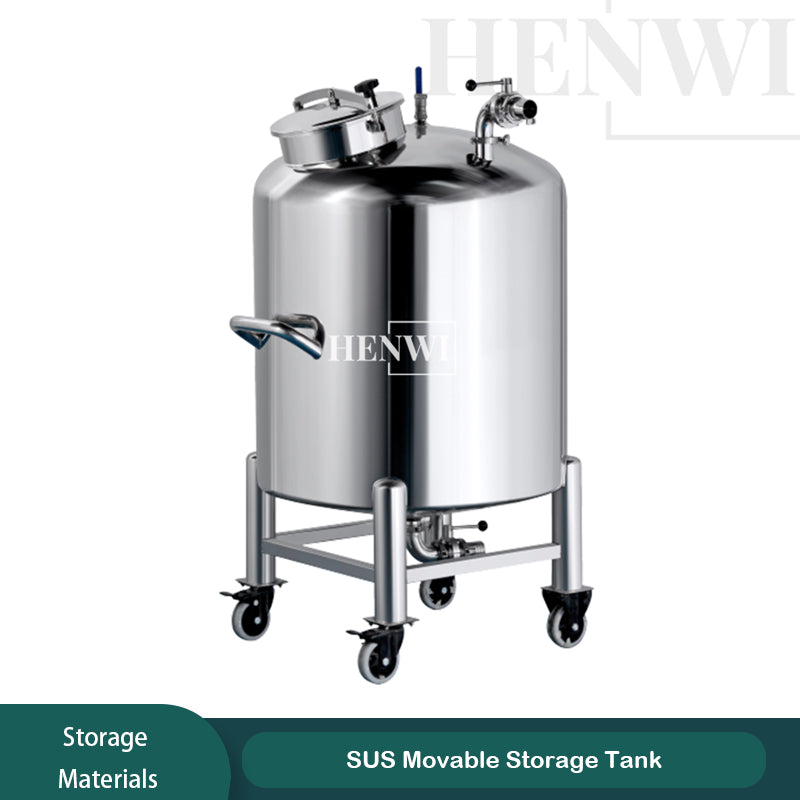
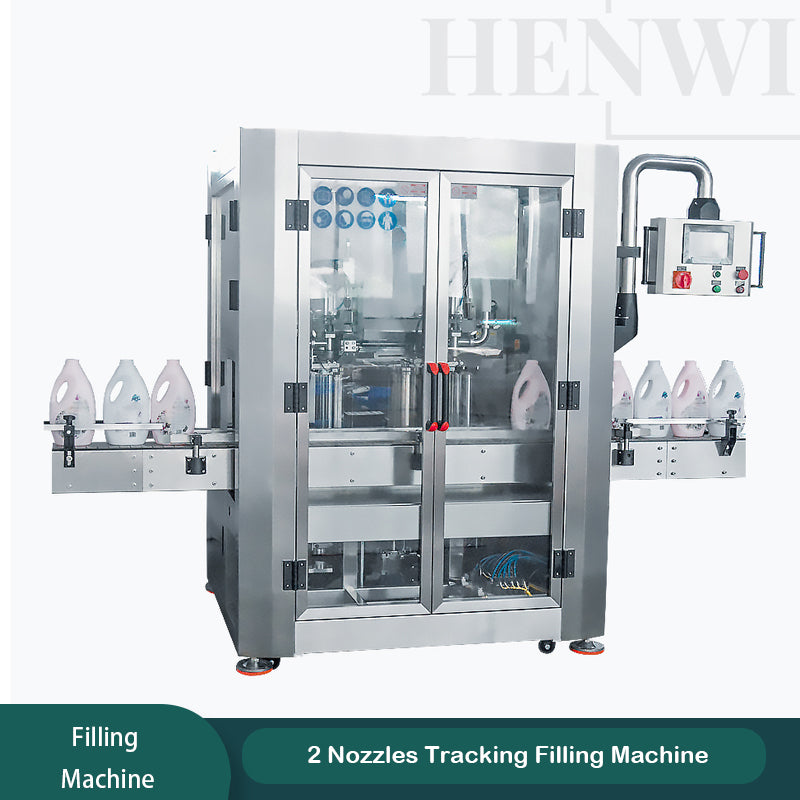
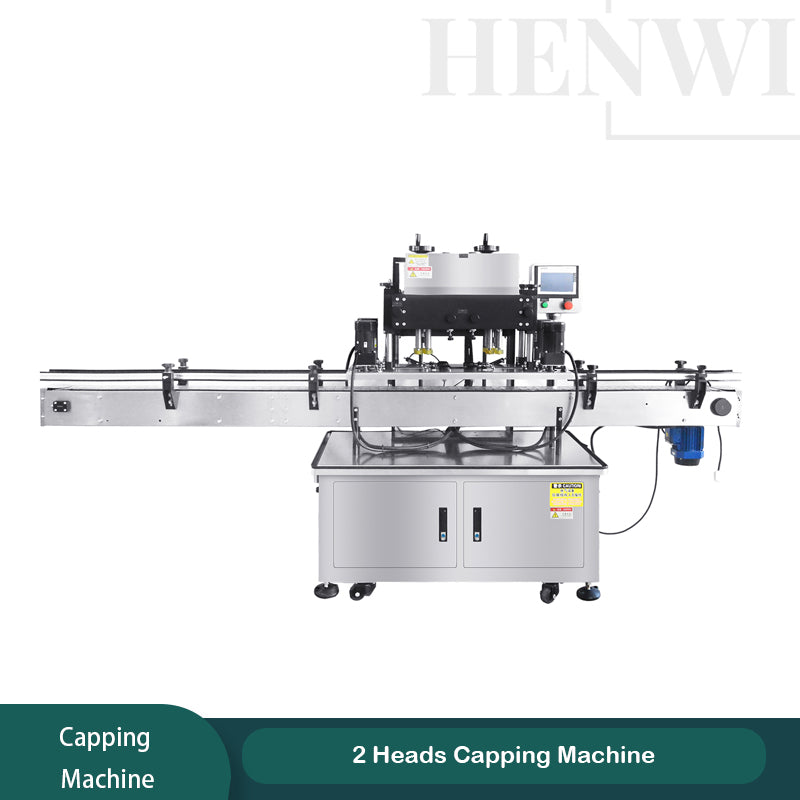
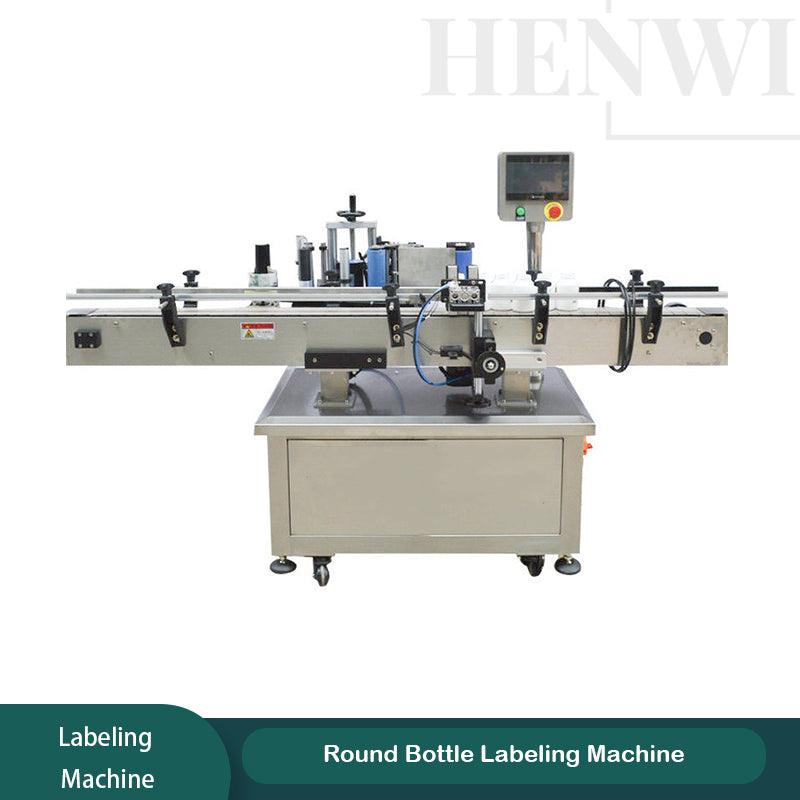
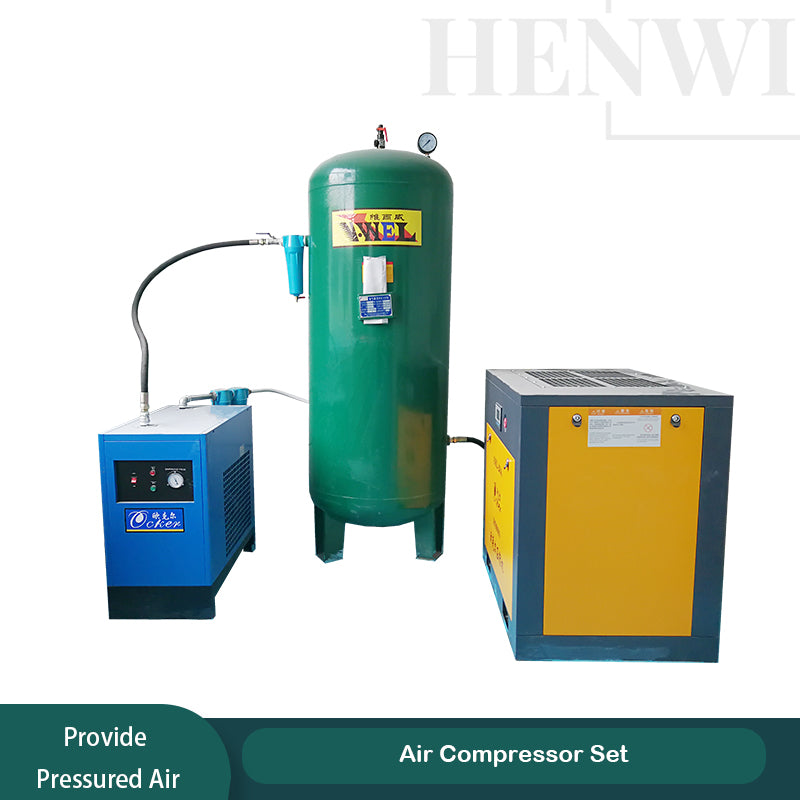
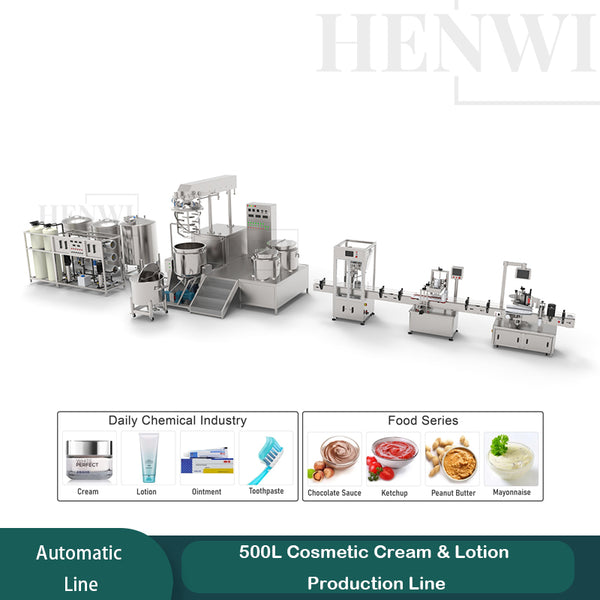
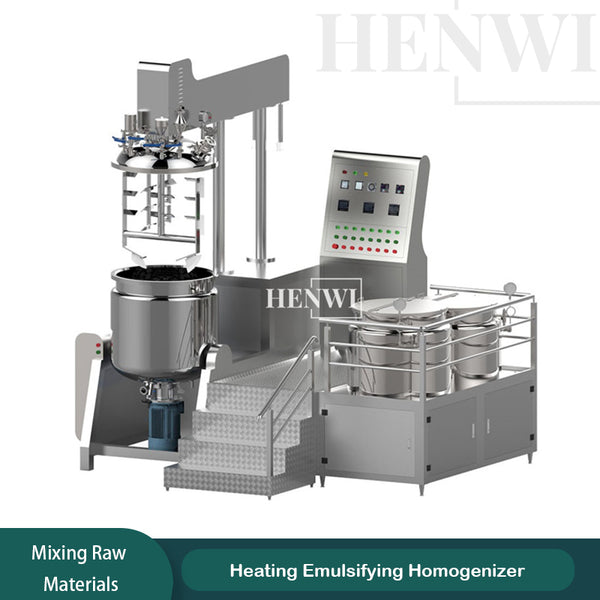
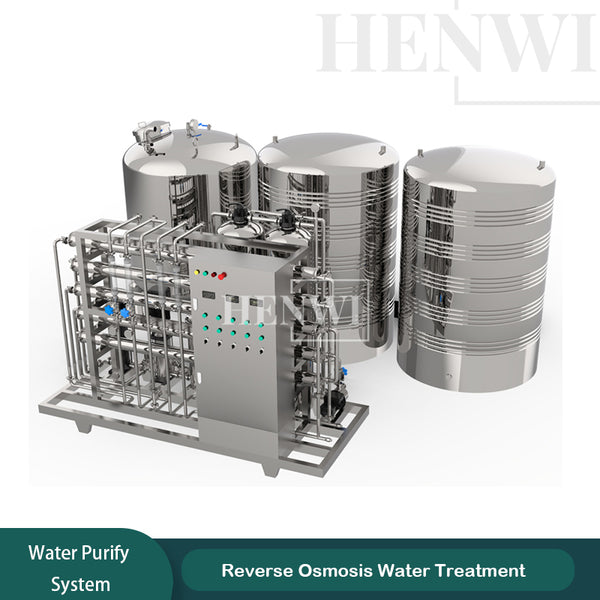
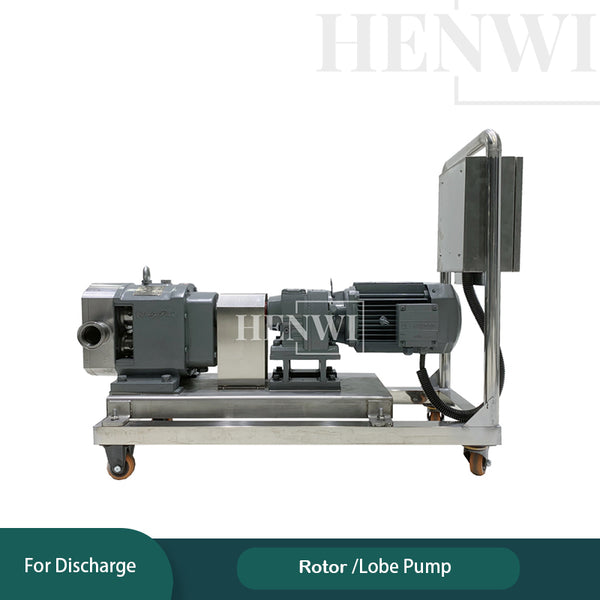
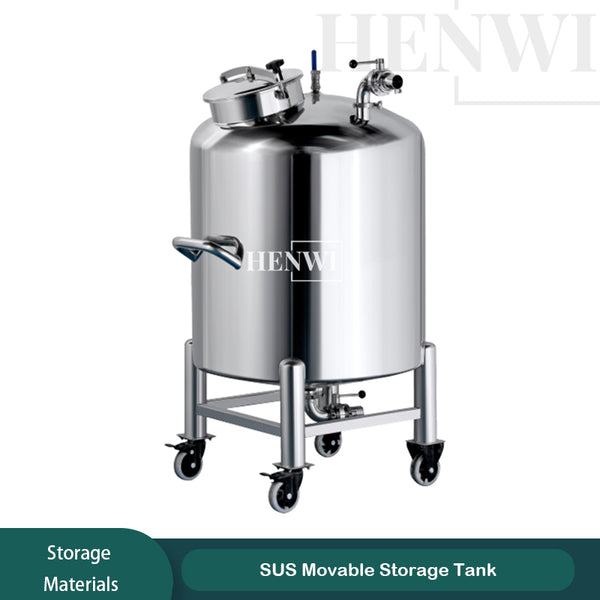
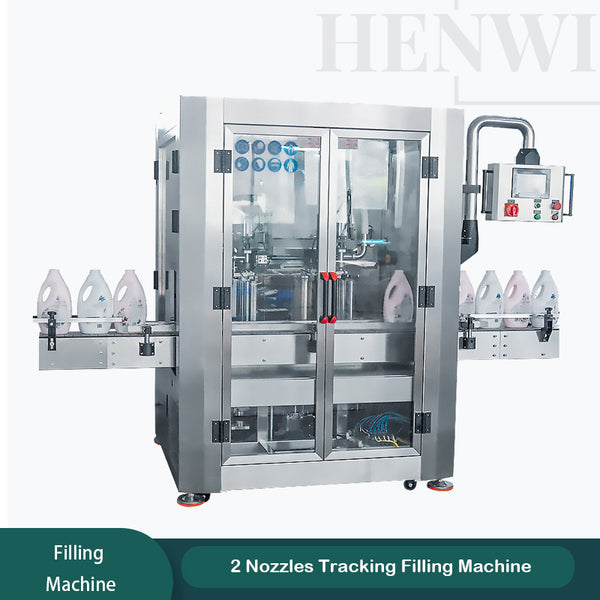
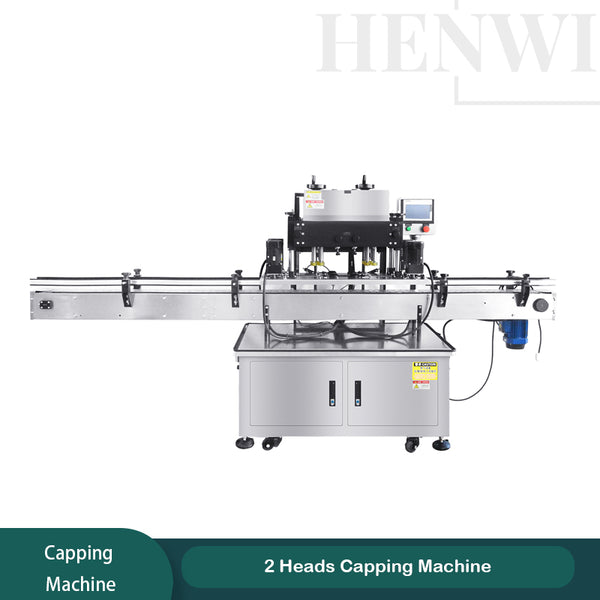
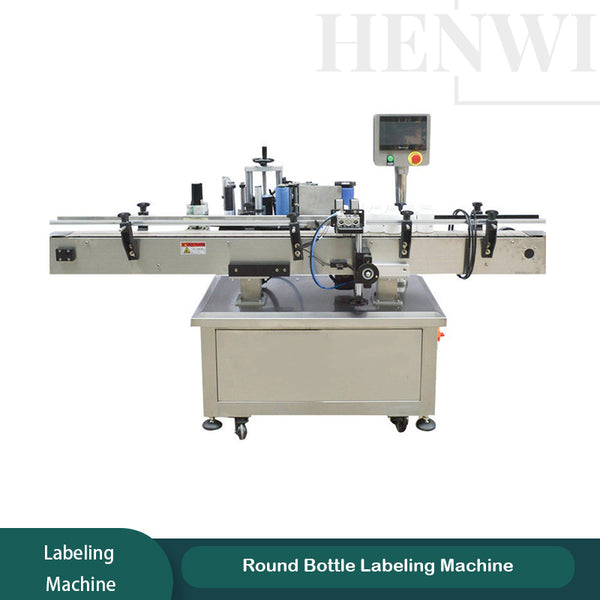
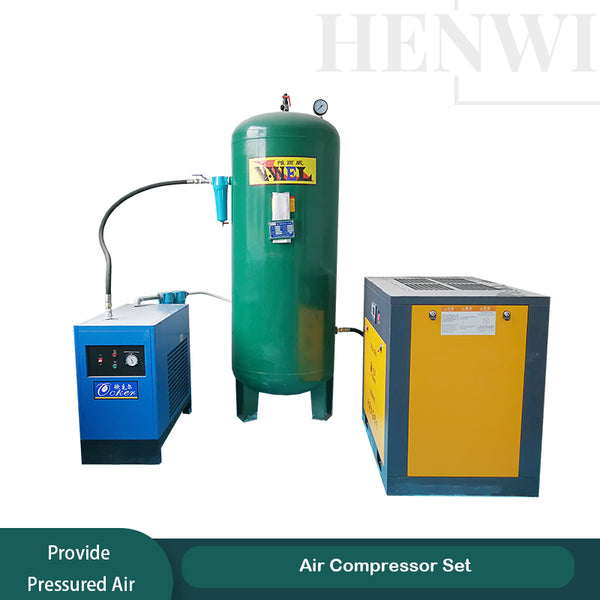
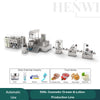
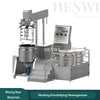
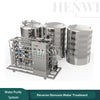
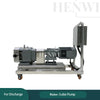
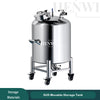
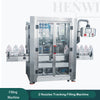
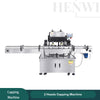

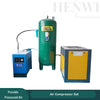
2000L semi-automatic cosmetic cream & lotion production line
- セール価格
- $59,000
- 通常価格
- $65,000
- 保存します
- $6,000 (10%)
This 500L cosmetic cream production line is a complete set of production equipment system, designed for the manufacture of cream cosmetics (such as cream, lotion, cream, etc.). The production line ensures efficient, accurate and high-quality cosmetic cream production through the cooperation of various equipment, including reverse osmosis water treatment system, vacuum emulsification system, discharge pump, storage tank, automatic filling machine, automatic capping machine, automatic labeling machine, coding machine and air compressor, etc.
Parameter
Model: HWPL-CL-500L |
Capacity: 500 Liters/Batch |
Time for per batch: 1-2hours (1500-2000Litres/Day) |
Output: 15000-20000bottles/day (100ml) |
Applicable bottle volume: 50-500ml |
Applicable bottle shape: Round |
Number of workers needed: 5-7people |
Total power: 90KW |
Voltage: 220V & 380V (can be customized) |
Total space: L15000*W6000*H4500mm |
Content
500L reverse osmosis water treatment * 1 set |
40W UV lamp * 1 set |
370W VDF water pump * 1 set |
1000L SS304 water tank * 1 set |
500L vacuum emulsifying mixer * 1 set |
4KW rotor pump * 1 set |
500L SS316 movable storage tank * 2 sets |
Pneumatic pump * 1 set |
Automatic 2 nozzles piston filling machine * 1 set |
Automatic capping machine * 1 set |
Automatic round bottle labeling machine * 1 set |
7.5KW air compressor set * 1 set |
500L/Hr Reverse Osmosis Water Treatment System |
In the cosmetics production line, the reverse osmosis water treatment system (RO system) is one of the key links to ensure that the water quality meets the production requirements. Water is the most widely used raw material in cosmetics production, and its purity directly affects the quality and stability of the product. Reverse osmosis technology can effectively remove impurities, microorganisms, heavy metals and ions in water to ensure the purity of water. ### Principle of reverse osmosis water treatment system: Reverse osmosis is a physical separation technology that filters water through a semipermeable membrane. Under high pressure, water molecules pass through the semipermeable membrane, while dissolved inorganic salts, organic matter, microorganisms and other impurities are intercepted, thereby obtaining high-purity water. Its working principle is as follows: 1. **Pretreatment**: Remove large particle impurities, residual chlorine and suspended solids through filtration, softening and dosing, and reduce membrane pollution. 2. **Reverse osmosis process**: The high-pressure pump presses the pretreated water into the reverse osmosis membrane system, the water molecules pass through the membrane, and the impurities are blocked on one side of the membrane, producing pure water (permeate water) and concentrated water (wastewater). 3. **Post-treatment**: Sometimes, RO water needs further treatment, such as UV sterilization or activated carbon filtration, to remove any residual microorganisms or organic matter. ### Importance of RO water treatment in cosmetic production: 1. **Ensure product quality**: RO water can prevent impurities in the water from adversely affecting cosmetic formulas, such as color change, uneven texture or shortened shelf life. 2. **Avoid microbial contamination**: RO can remove bacteria and viruses from water to prevent cosmetics from being contaminated during production and storage. 3. **Extend equipment life**: Pure water reduces mineral precipitation in pipes, containers and production equipment, reduces corrosion and clogging of equipment, and extends the service life of equipment. ### Requirements for water quality in the cosmetics industry: According to relevant standards of the cosmetics industry, production water must meet pharmaceutical grade or high purity requirements. RO treated water is usually further passed through a secondary RO or electrodeionization (EDI) system to ensure that it meets ultrapure water standards for the production of high-end skin care products, essences and other products. |
500L Vacuum Emulsifying Mixer |
The vacuum emulsifier is one of the core equipment in the cosmetics production line, which is specially used to mix, disperse, homogenize and emulsify liquid, semi-solid or paste materials. It is often used to produce high-viscosity or multi-phase system cosmetics such as skin creams, lotions, facial masks, essences, etc., which can ensure the uniformity and stability of the products. ### Working principle of vacuum emulsifier: ### Structural composition of the vacuum emulsifier: ### Main features of vacuum emulsifier: |
4KW Rotor Pump |
The discharge rotor pump is a commonly used conveying equipment in the cosmetic production line, which is specially used to convey high-viscosity materials from one process stage to the next process. It is widely used in cosmetic production, especially for conveying high-viscosity products such as lotions, creams, essences, shampoos, etc., to ensure that the material flows smoothly and efficiently throughout the production process. ### Working principle of the discharge rotor pump: ### Main features of the discharge rotor pump: ### Structural composition of the discharge rotor pump: |
500L Movable SUS316 Sealed Lid Storage Tank |
Mobile sealed storage tanks are important equipment for storing and transporting raw materials or semi-finished products in cosmetic production lines. The tanks are usually designed with stainless steel and equipped with sealing covers and mobile devices, which can be easily moved between various processes of the production line while maintaining material stability and preventing contamination. ### Structural features of mobile sealed storage tanks:
|
Automatic Tracking Piston Filling Machine |
The fully automatic tracking piston filling machine is a device used in the cosmetics production line for efficient and accurate filling of liquids, lotions, pastes and other materials. It is especially suitable for products with high viscosity, such as creams, lotions, shampoos, essences, etc. The main feature of this equipment is the "tracking" filling method, that is, during the filling process, the filling head can run synchronously with the movement of the container to ensure that the filling process is continuous, smooth and efficient. ### Working principle of the fully automatic tracking piston filling machine: ### Main features of the fully automatic tracking piston filling machine: 1. **Automatic adjustment to bottles of different sizes**: The size formula of different bottles is stored on the touch screen, and the machine can achieve one-click adjustment. |
Automatic Capping Machine |
The fully automatic double-head four-wheel capping machine is an important equipment for automatically locking bottle caps in cosmetic production lines. It is suitable for bottles of different sizes and shapes and is widely used in the packaging process of skin care products, cosmetics, shampoo, lotion and other products. The "double head" of the equipment refers to the two capping heads at the same time, which can handle two production lines at the same time or perform double capping operations; "four wheels" refers to the use of four locking wheels to evenly press the bottle caps when locking the caps to ensure that the bottle caps are firmly and accurately locked. ### Working principle of the fully automatic double-head four-wheel capping machine: ### Main features of the fully automatic double-head four-wheel capping machine: 1. **Dual-head design**: The equipment is equipped with two independent capping heads, which can handle two production lines at the same time, or perform double capping operations, which improves production efficiency and is especially suitable for mass production needs. |
Automatic Round & Flat & Square Bottle Labeling Machine |
The round and flat bottle double-sided labeling machine is a device used for automatic labeling in the cosmetic production line. It is suitable for containers of various shapes, such as round bottles, flat bottles, etc., and can accurately attach labels on both sides of the bottle at the same time. This equipment is usually used in the packaging process of cosmetic products, such as skin creams, shampoos, shower gels, essences, etc. The efficiency and accuracy of the labeling machine greatly improve the automation level of the production line and the packaging quality of the products. ### Working principle of the round and flat bottle double-sided labeling machine: ### Main features of the round and flat bottle double-sided labeling machine: 1. **Double-sided labeling**: The equipment is equipped with two sets of labeling systems, which can label both sides of the bottle at the same time, especially suitable for products with double-sided labels (such as cosmetic bottles with different front and back labels). |
7.5KW Screw Air Compressor Set |
Screw air compressor is one of the key equipment in the cosmetics production line. It is mainly used to provide compressed air to drive various pneumatic equipment in the production line. In the process of cosmetics production, compressed air is widely used in the operation of equipment such as filling machines, labeling machines, emulsifiers, etc. Screw air compressors ensure the efficient, continuous and stable production process through stable compressed air output. ### Working principle of screw air compressor: ### Main features of screw air compressors: |
Shipping Information
Shipping
In order to offering better service,we have operated with multiple shipping companies like Fedex,DHL,DUP,UPS,EMS etc.We sure that you can choose the most suitable one.For our online products.
1.Most of them will be shipped by express shipping like Fedex or DHL,delivery time is 6-8 business days.
2.Some small products will be sent by regular shipping,delivery time is 15-45 business days.(There is an instruction saying this product will be sent by regular shipping.)But if you need faster shipping,please contact us to upgrade shipping method.We are glad to help you.
3.Some customers can not place their order since there is an error saying that we can not delivery the product to their countries.If you are in this situation,please contact us to confirm the price and shipping,we will help you place the order successfully .The shipping fee is hard to set up online,and in this situation,it is possible to spend less money to get this product,so it will be better if you can contact us.
4.If you find the shipping fee is too expensive for you,please contact us,we are glad to help you find the best shipping method.For large machine,it will be better for you to contact us before placing the order,in this way we can confirm the price,delivery time and check if the machine is really suitable for your products.
Payment
You may find that we only support paypal now,but we can offer other payment method like west union,TT,credit card,wechat pay,Alipay.You will find the best one as your need.If you have any problems about payment,please send us message.Although Some of them are not supported on online service now, we are trying our best to upgrade these.
Product Service
We want you to be happy with your purchase and trying our best to offer the better service to our customers,so we offer some solution if you have below problems or meet below situation: 1. If you received a machine and found the machine was broken :
First,we should note that we will not send any used machine or broken machine to our customers.As we all know,everything will happen during shipping,if your machine is broken,please contact us and help us to complaint this to shipping company.We are here to help you.
2. If you don’t know how to assemble machine or use the machine :
Some of our machine may need you assemble them,or you don’t know how to use the machine,just send us e-mail or message,we will send you video and manual to help you know more about it.
Accuracy, completeness and timeliness of information
We are not responsible for any inaccurate, incomplete or timely information provided on this website. The materials on this website are for general information only and should not be relied upon or used as the sole basis for making decisions without consulting primary, more accurate, complete or timely sources of information. Any reliance on the materials on this website is at your own risk. This website may contain certain historical information. The historical information is not necessarily up to date and is for your reference only. We reserve the right to modify the content of this website at any time, but we are under no obligation to update any information on our website. You agree that it is your responsibility to monitor changes to our website.
Service and price modification
The prices of our products are subject to change without prior notice. We reserve the right to modify or terminate the Services (or any part or content thereof) at any time without notice. We shall not be liable to you or any third party for any modification, price change, suspension or discontinuation of the Services.
Products or Services
Some products or services may be available online only through the website. These products or services may be available in limited quantities and can only be returned or exchanged in accordance with our return policy. We have made every effort to display the colors and images of our products that appear in stores as accurately as possible. We cannot guarantee that any color displayed on your computer monitor is accurate.
HENWI TECHNOLOGY LIMITED
[Re: Privacy Compliance Officer]
Bldg 3, Gaoyi Industrial Park, No.5 Shangbai Rd., 528226 Shishan town, Nanhai Dist, Foshan City, P.R., China
About Us
We are a professional cosmetic, pharm and food machinery production, sales and related technical services of modern high-tech enterprises.